Left: Galaxy Cluster Abell 370. NASA, ESA, and STScI
Right: Pyroxene crystals in a shale and ash glaze. Will Keating
“By cajoling and flattering their raw materials … the full character and beauty of those materials was brought into play…”
Michael Cardew
Graduation Exhibition
Clay College, Stoke-on-Trent, Aug 2024
My two years of study culminated in an exhibition of thrown and hand-built pottery, focused on a number of local clays, rocks and plant ashes sourced and tested during that time. Work was fired in a number of different ways to explore the potential of a limited palette of materials local to Stoke-on-Trent.
Some works were left unglazed and fired in a traditional wood-fired anagama kiln, others fired in electric kilns.
The bulk of the work was glazed and fired in a raw-brick, catenary arch gas kiln which I built especially for the exhibition, detailed in the following section.
“I prioritise self-sufficiency in my work, finding and processing my own clay and rocks, as well as building my own kiln from raw materials…
…the essential, geological nature of the material is maintained: communicated through the vocabulary of clay, rock and fire.”
— from Graduation Exhibition Catalogue


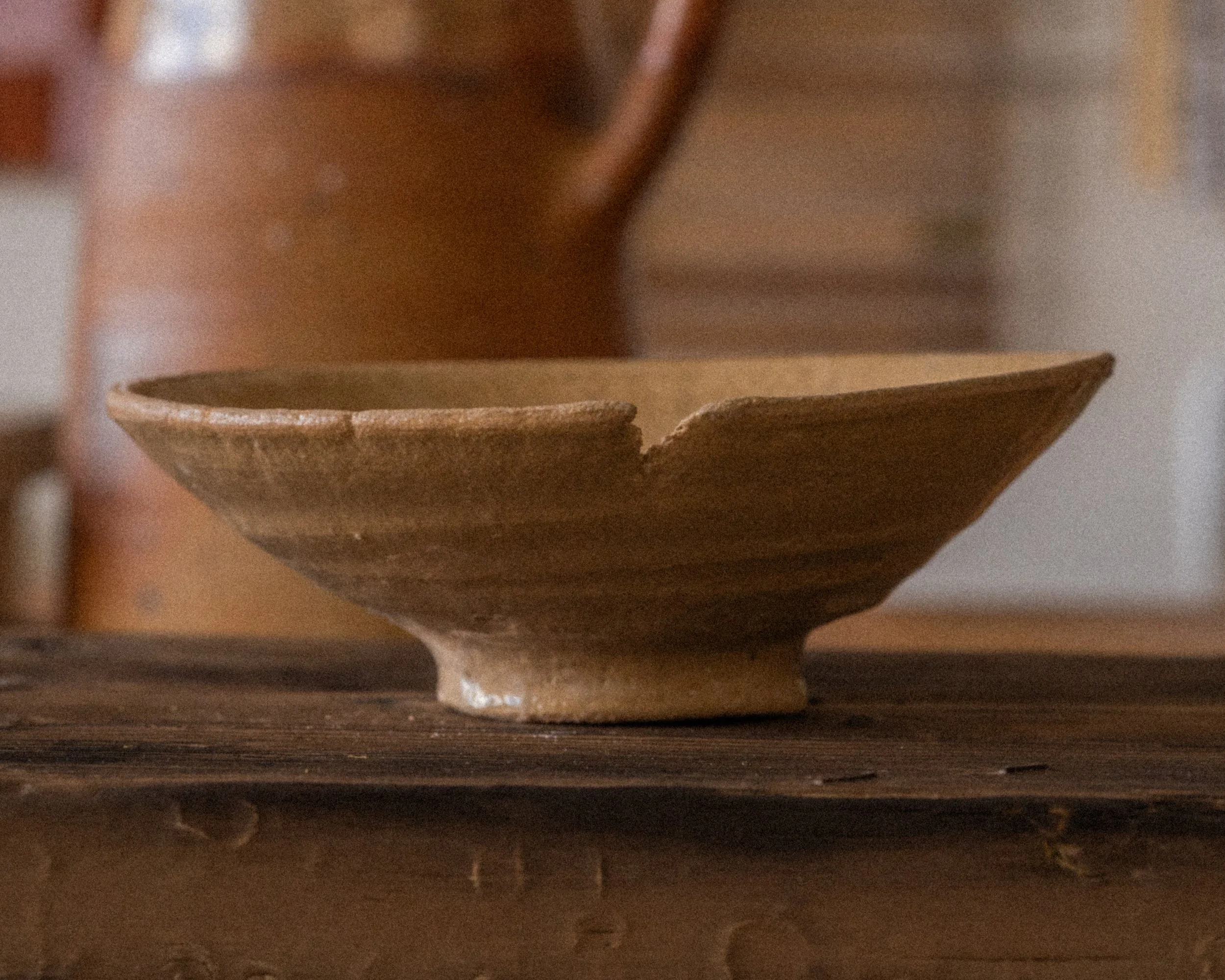
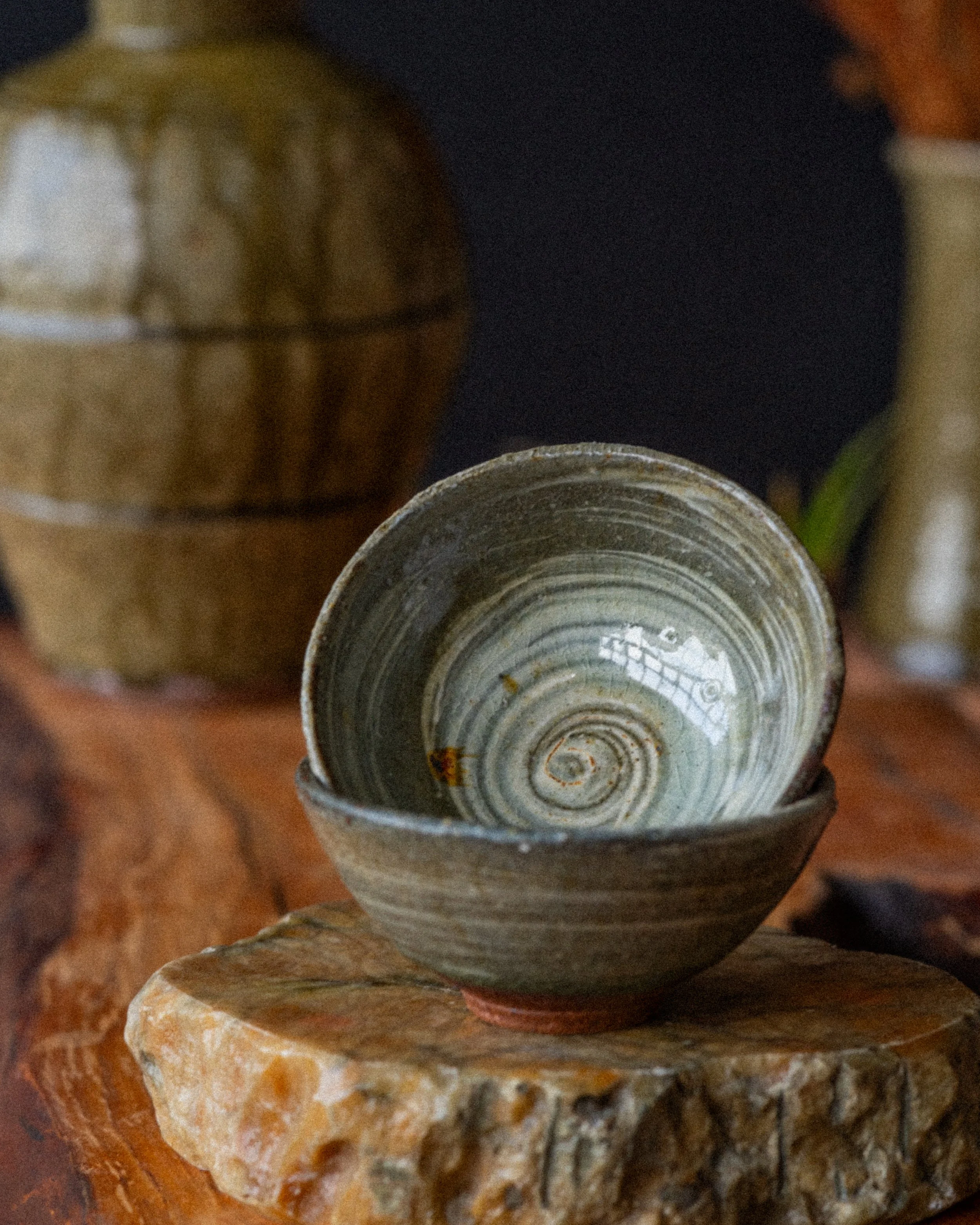
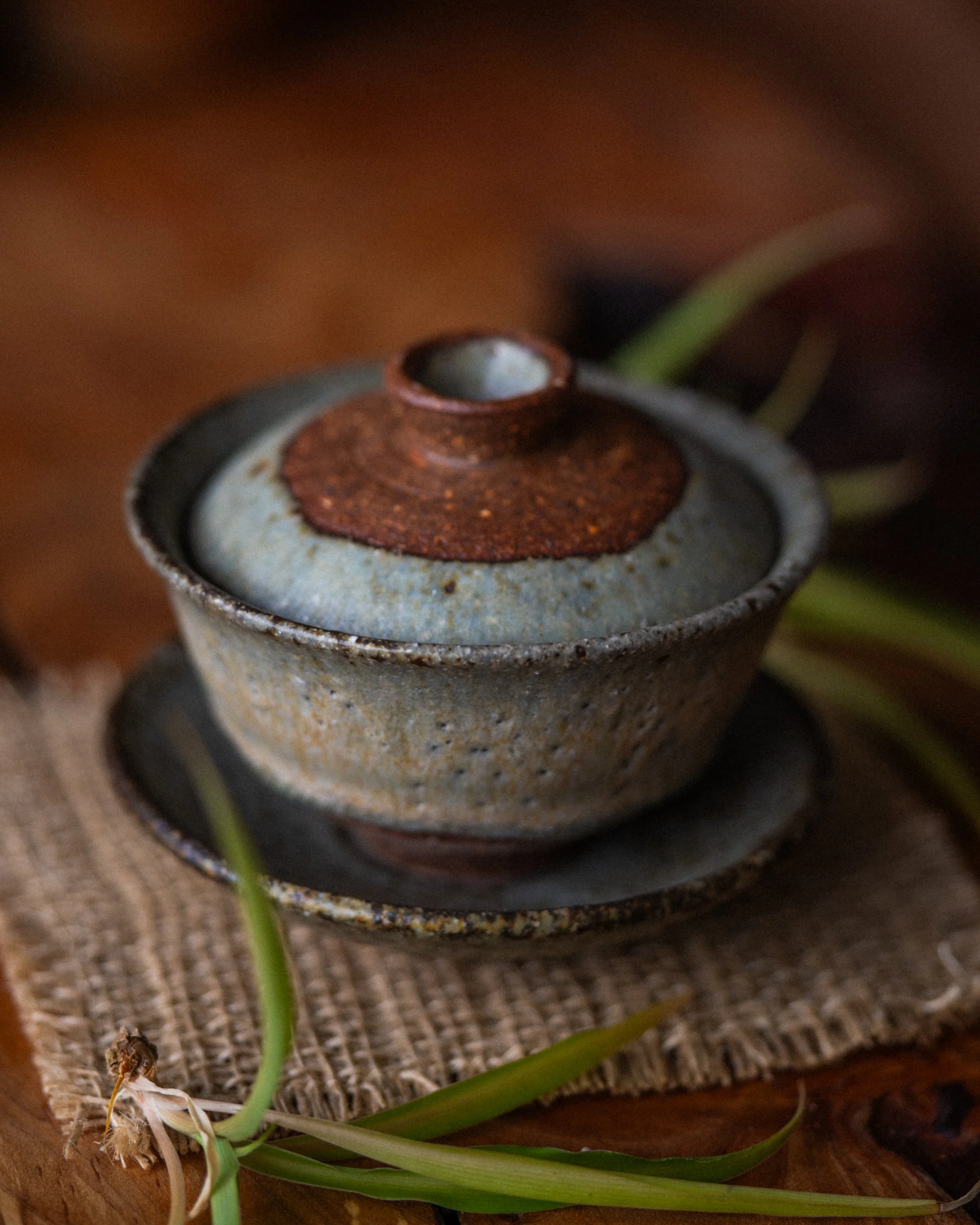
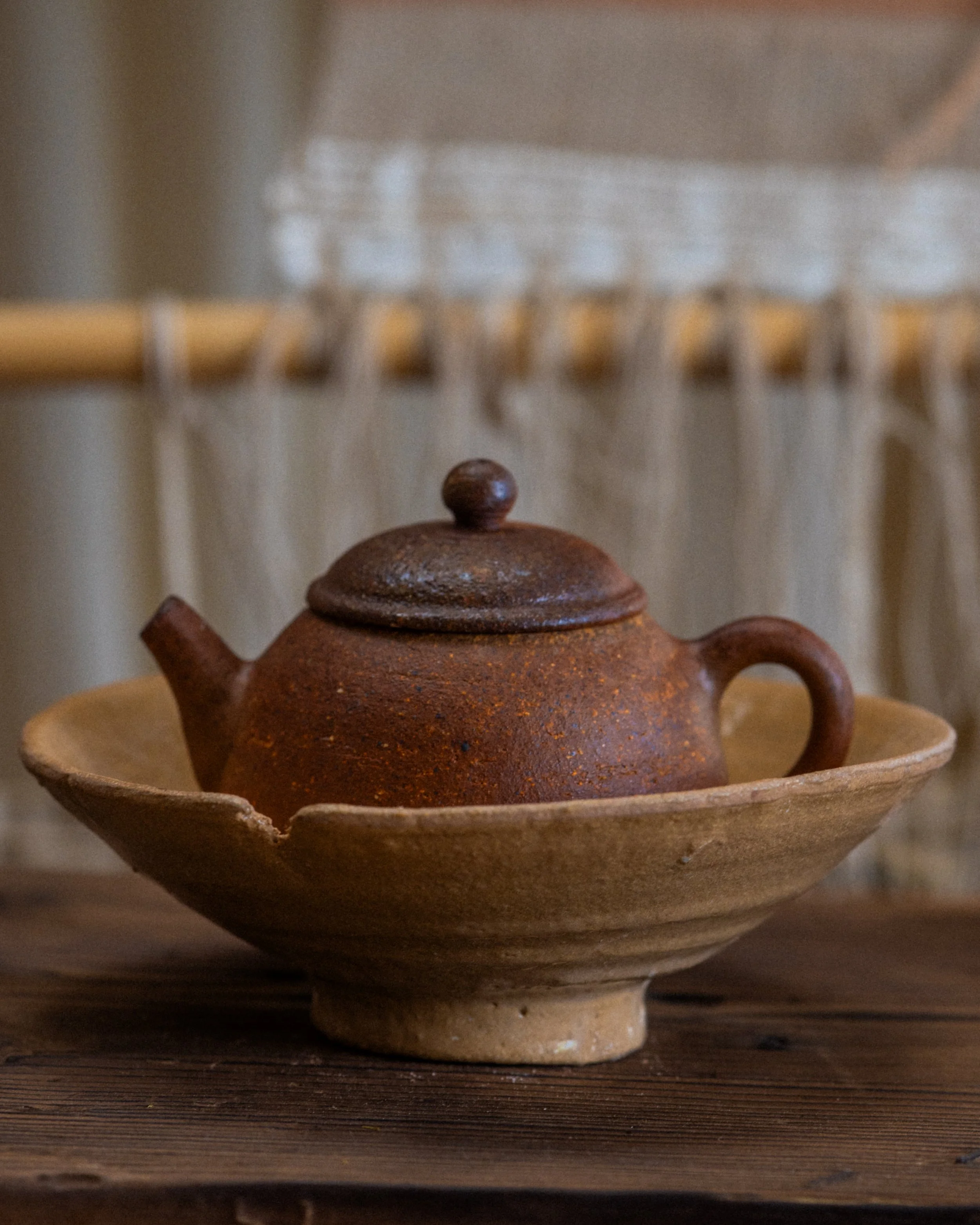
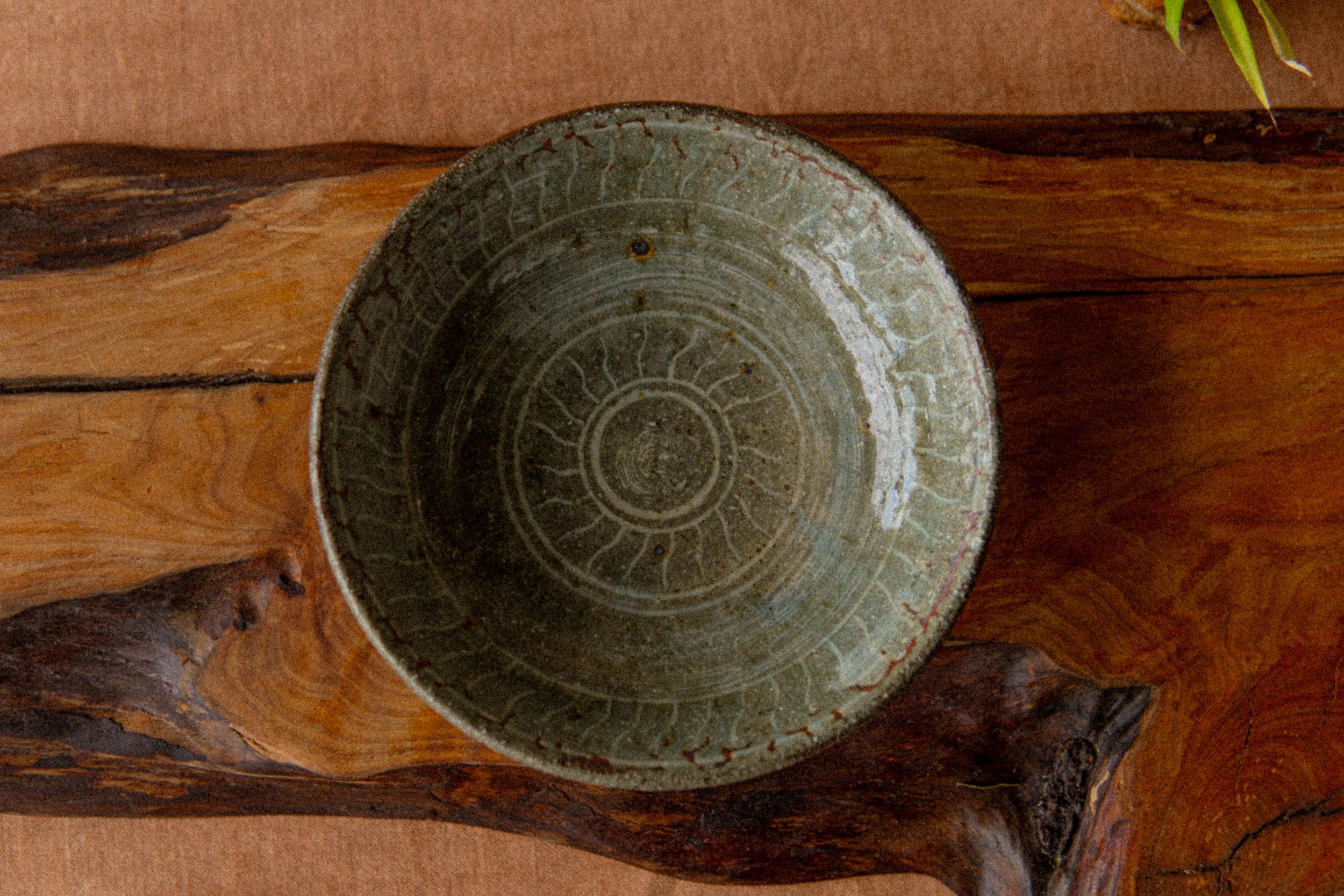

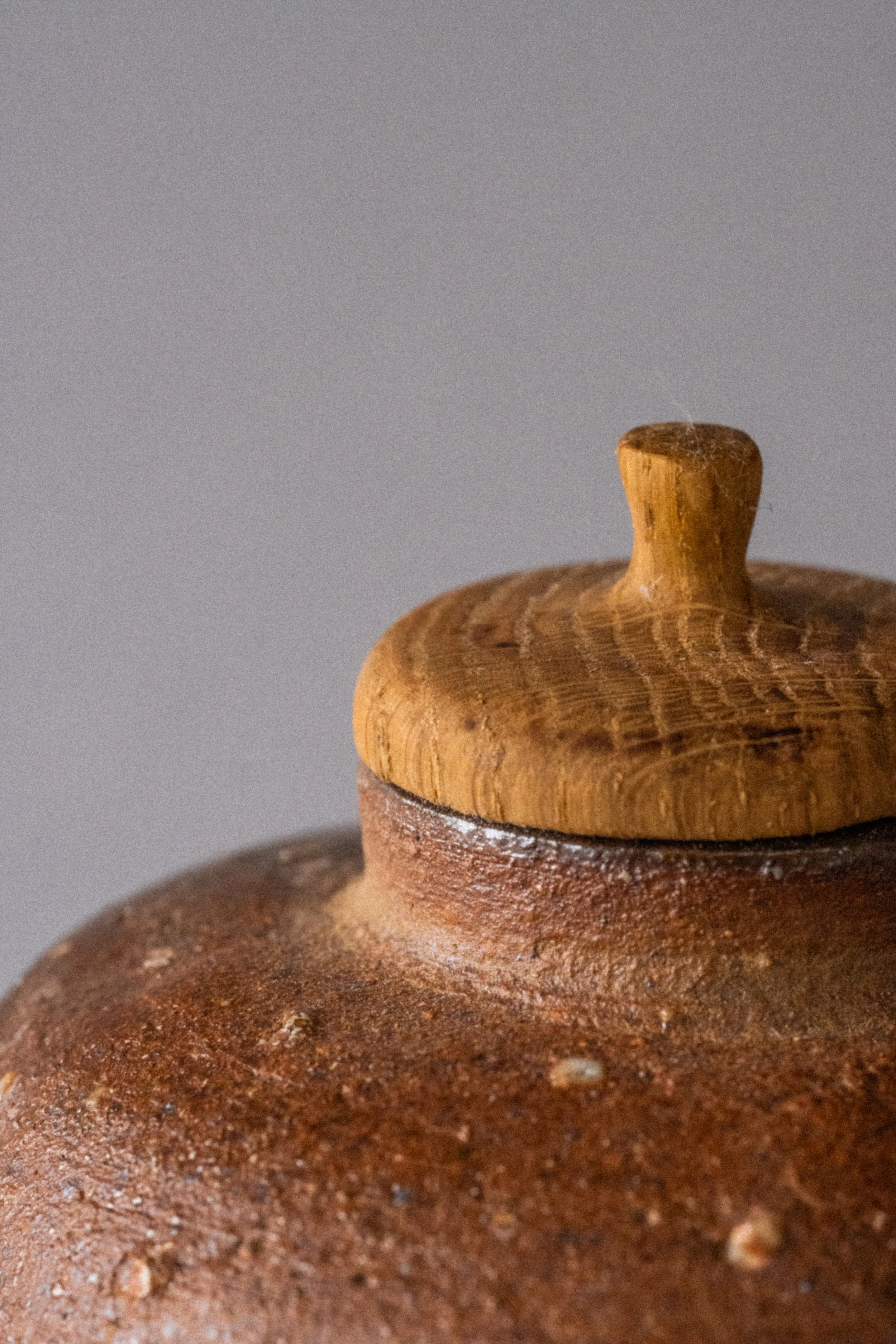

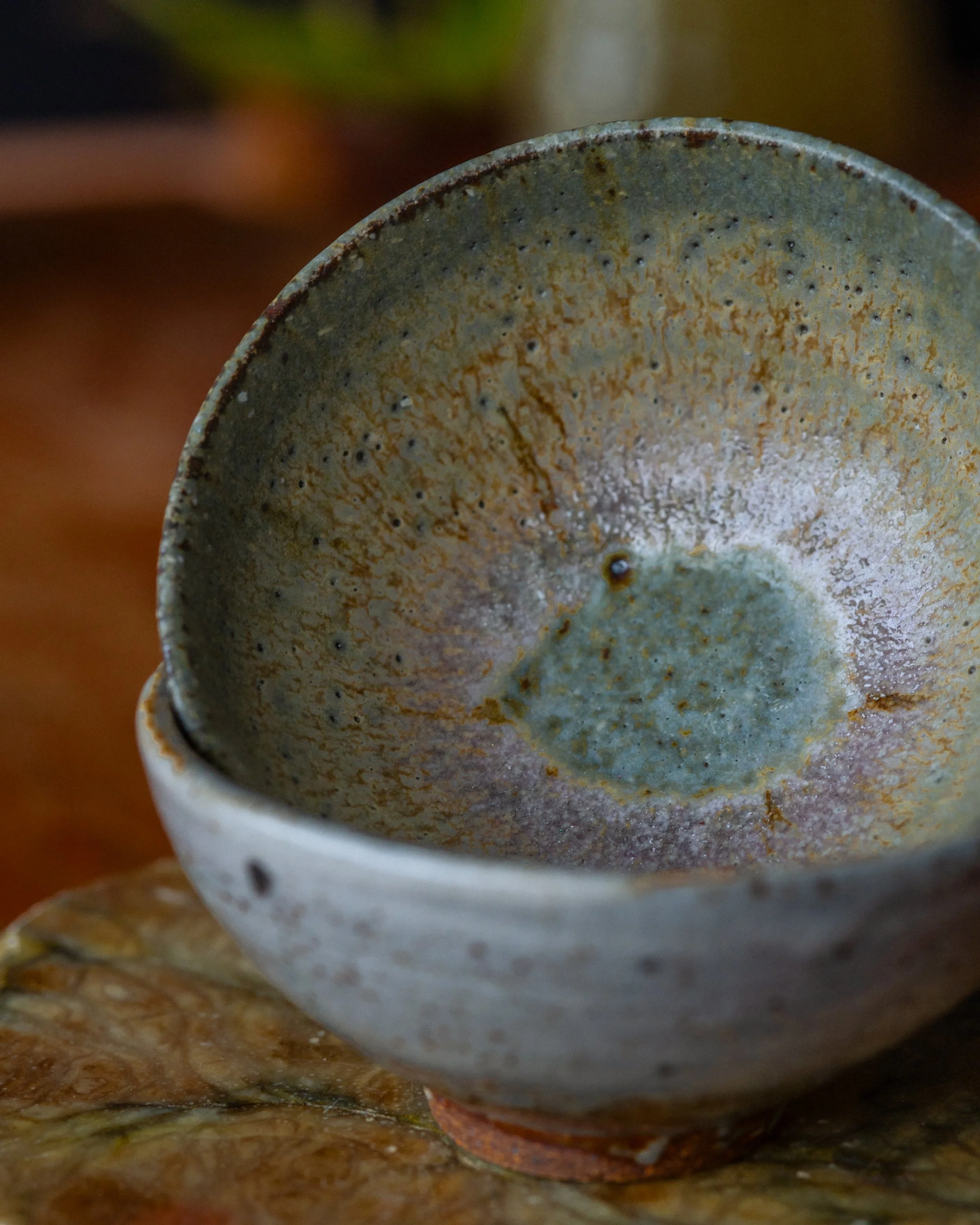
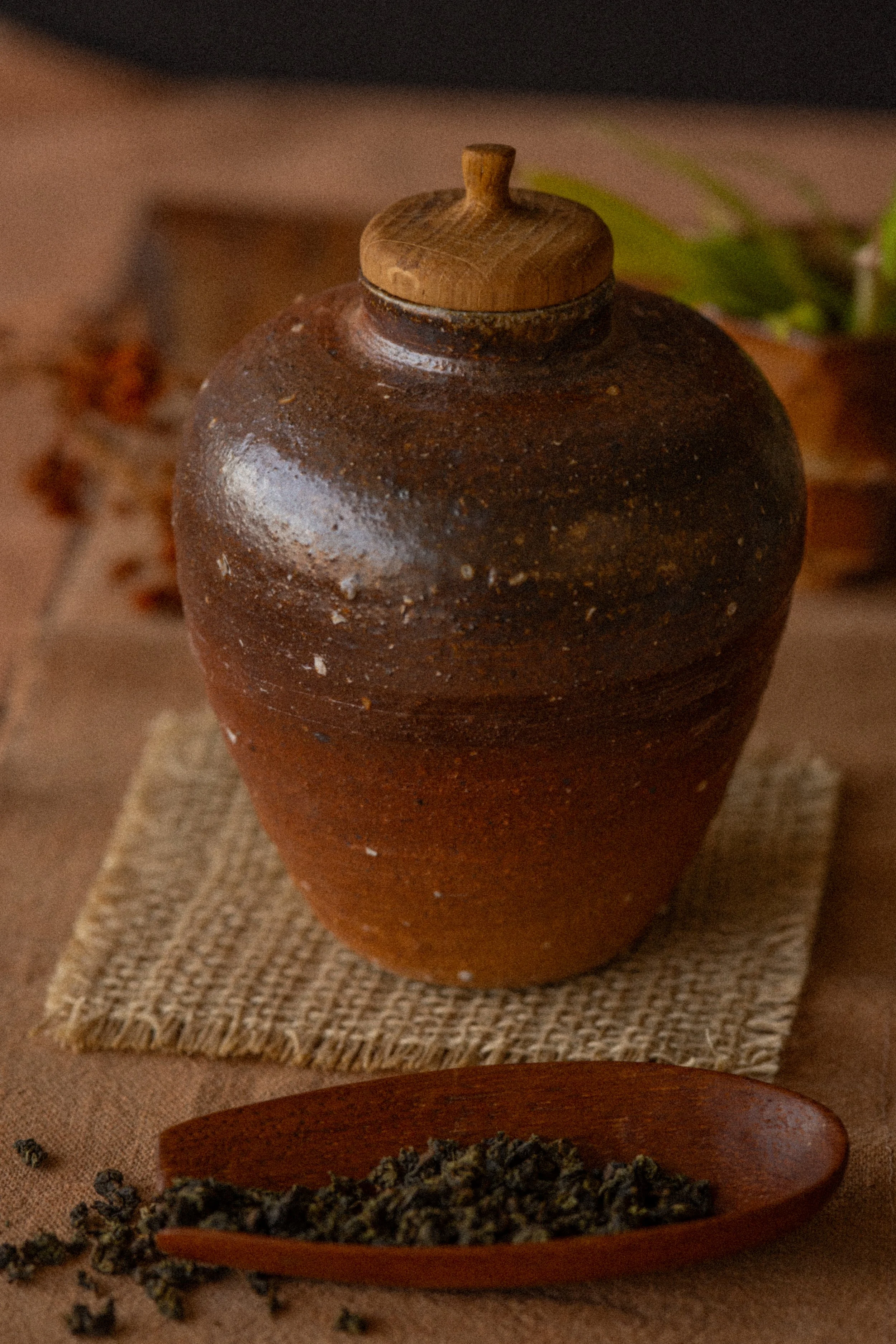

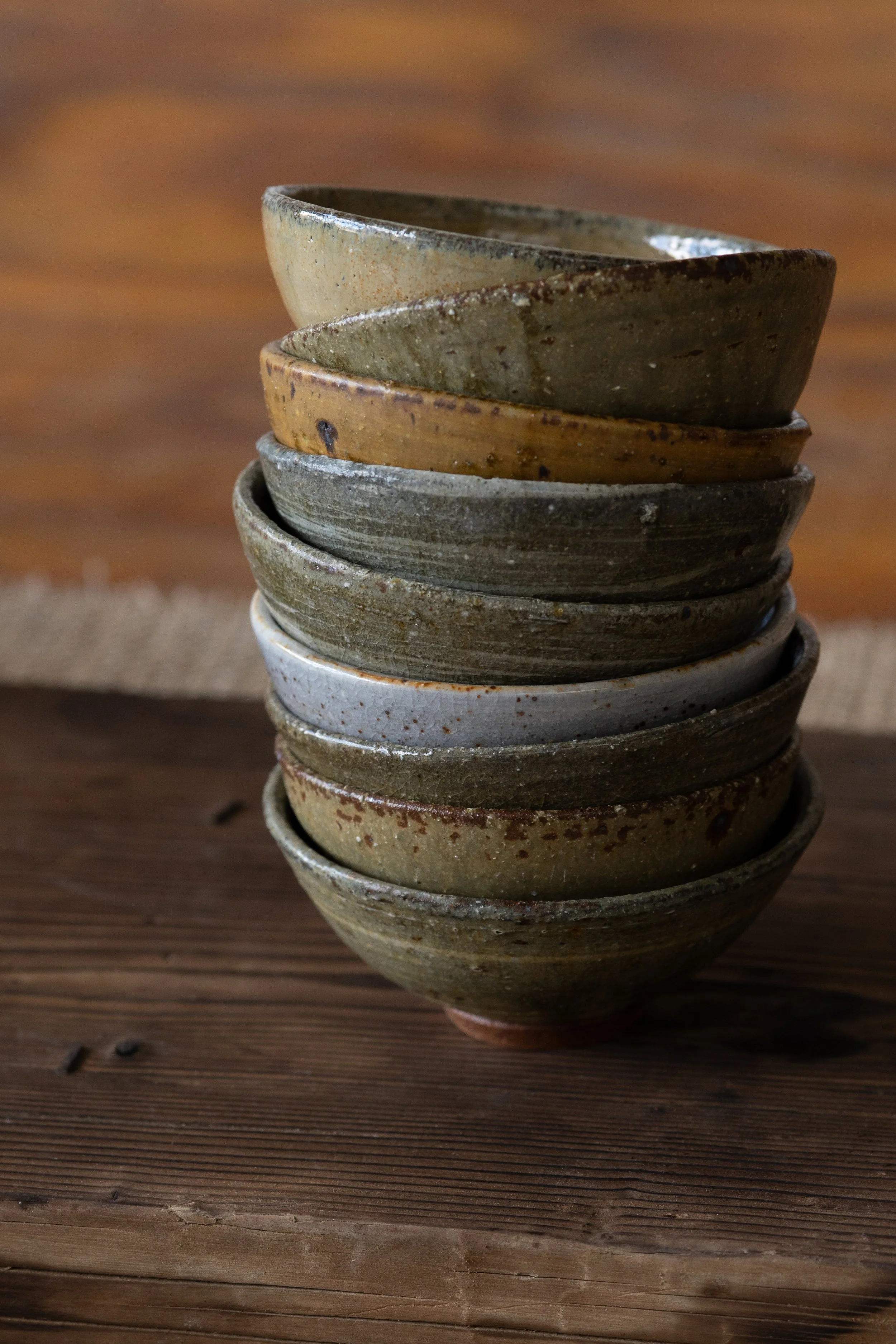

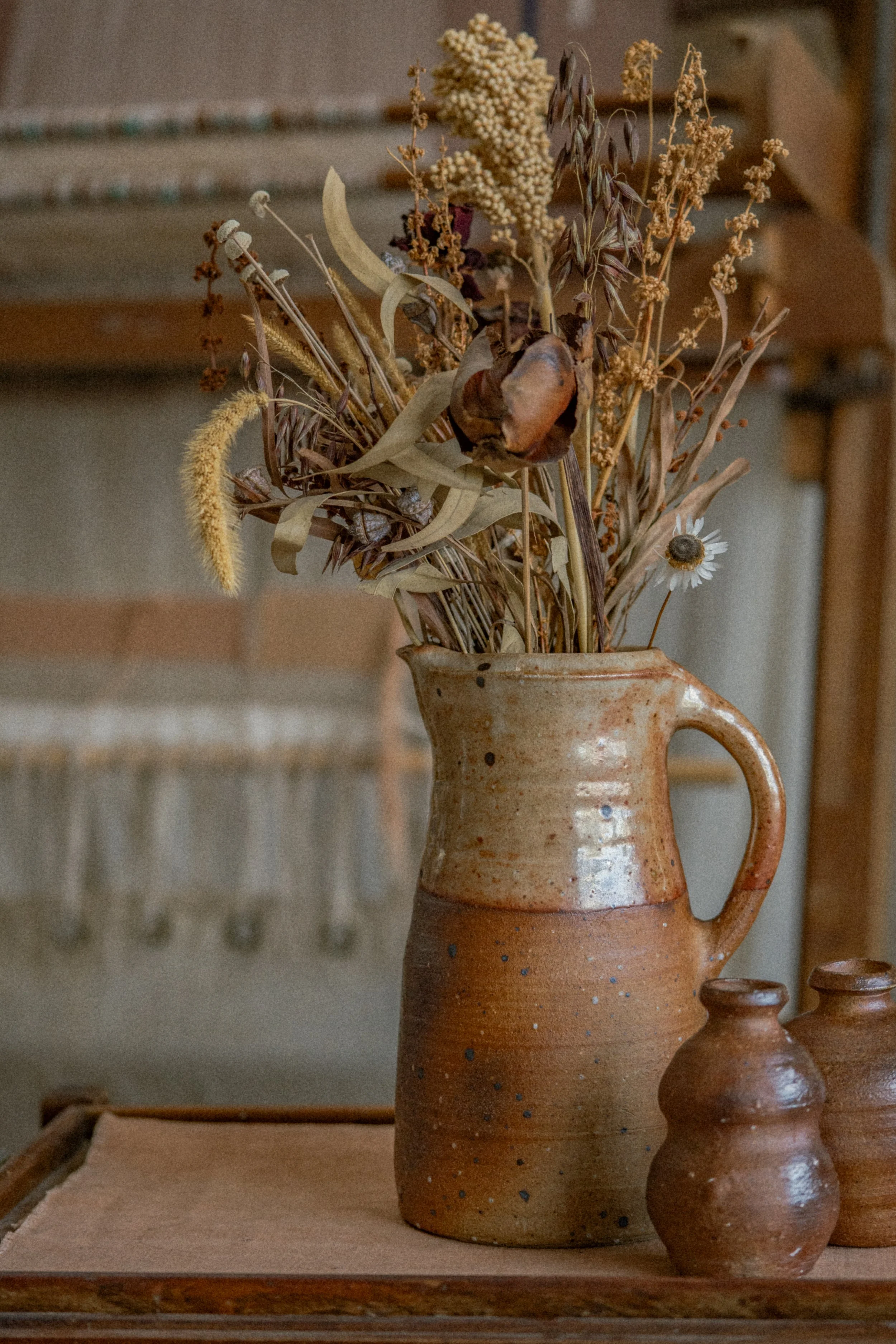
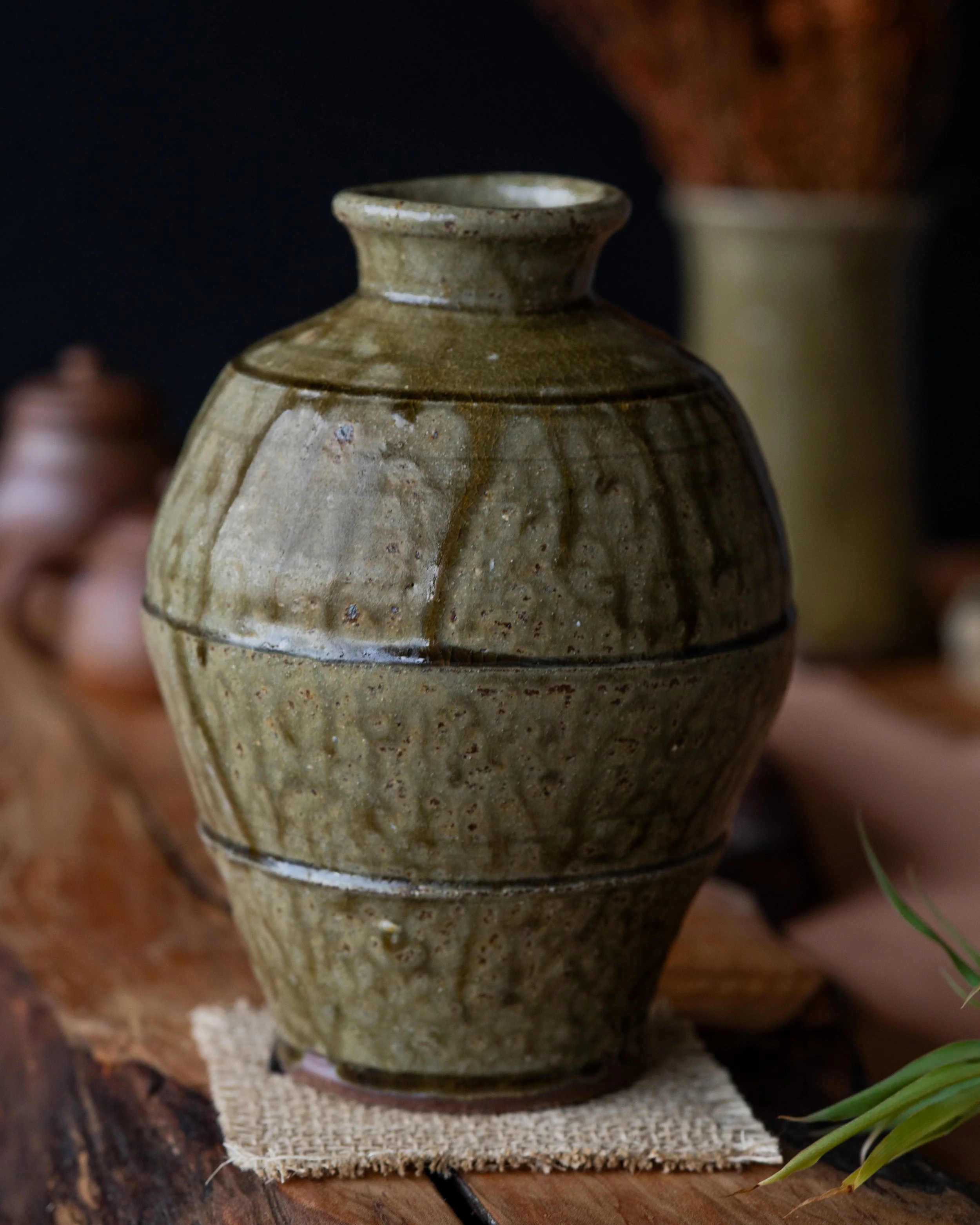

Catenary Arch Kiln
Clay College, 2024
With every project, I consider how best to combine traditional making techniques with modern technology. The finest ceramic works throughout history have been defined by the materials that were available to the potter. I believe that these limitations inspired creative growth, and in the age of mass consumption and availability, sometimes limits must be self-imposed.
Applying this thought to kiln-building, I set out to build a propane-fired kiln using as little virgin-material as possible. The insulating bricks used to build the kiln were hand-formed using over 70% recycled waste products from local industry. In taking this “back-to-basics” approach, I find that the result is, without fail, a better understanding of the subject matter, a truer understanding of how a kiln operates under the intense heat of the flames.
The bricks were laid in the unfired state, and the kiln gradually taken up to 1300 degrees over the course of three firings, hardening it in place. The kiln successfully fired to Cone 11 in around 13 hours.
This video shows the whole process, from making the bricks to the firing of the kiln.




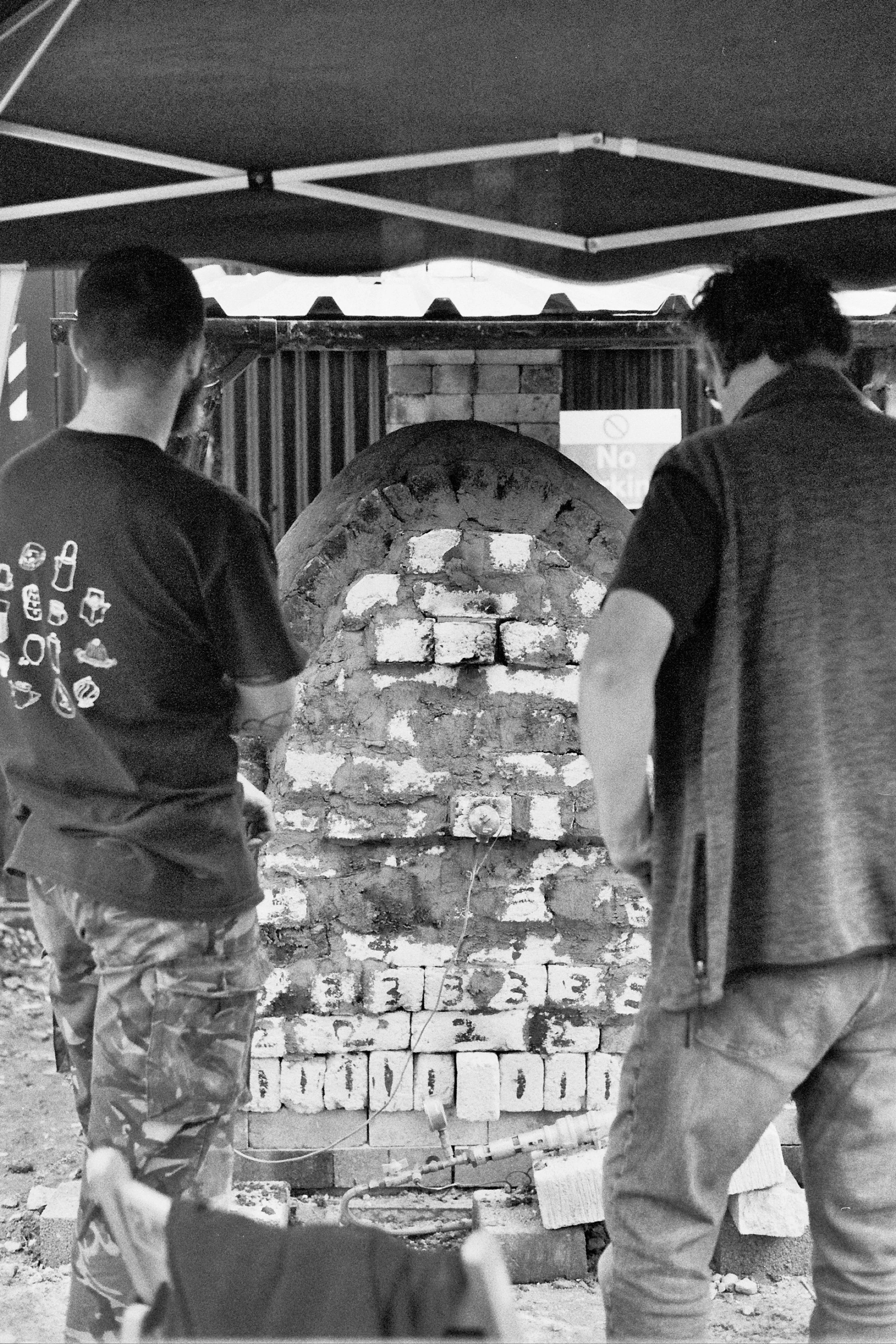
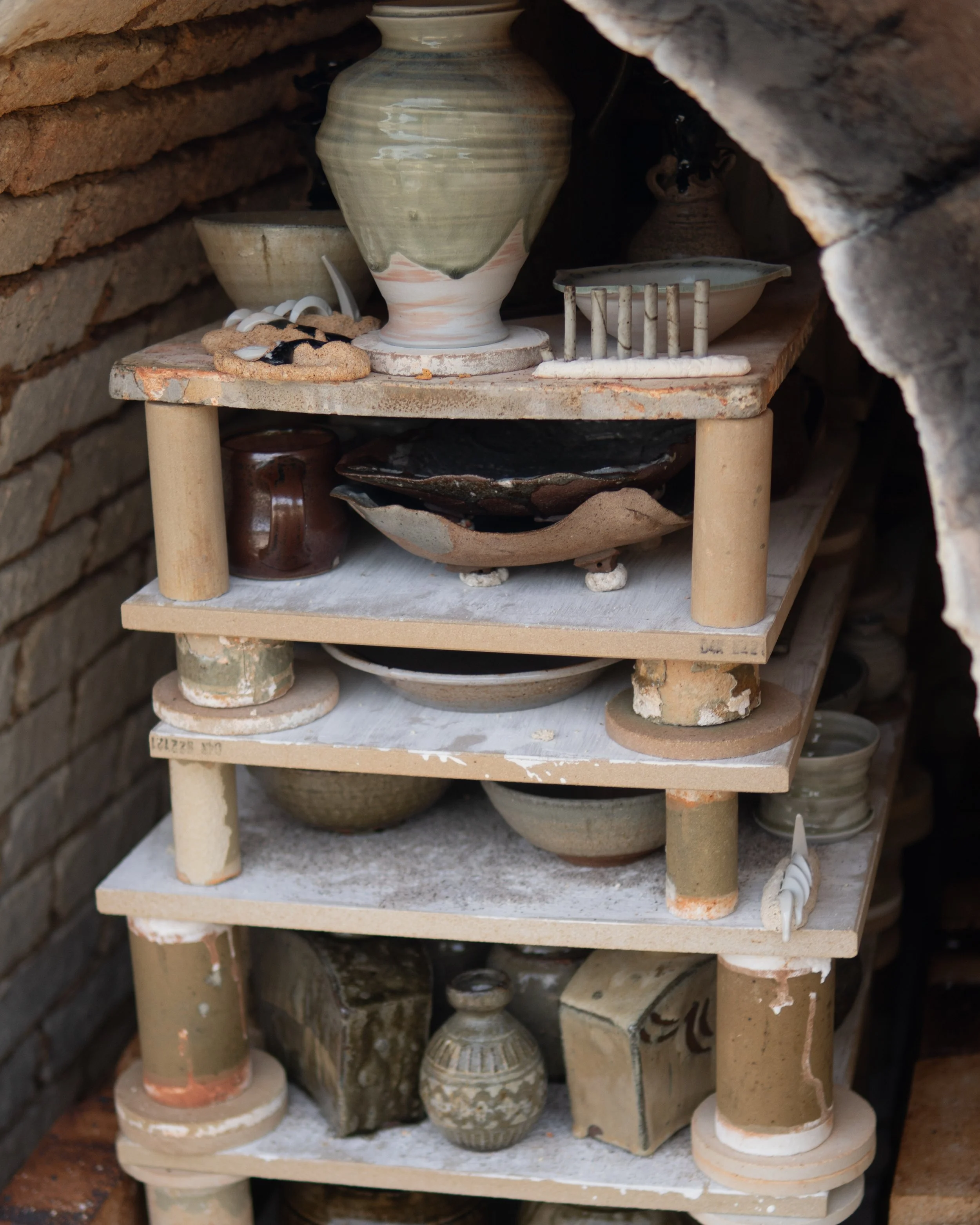
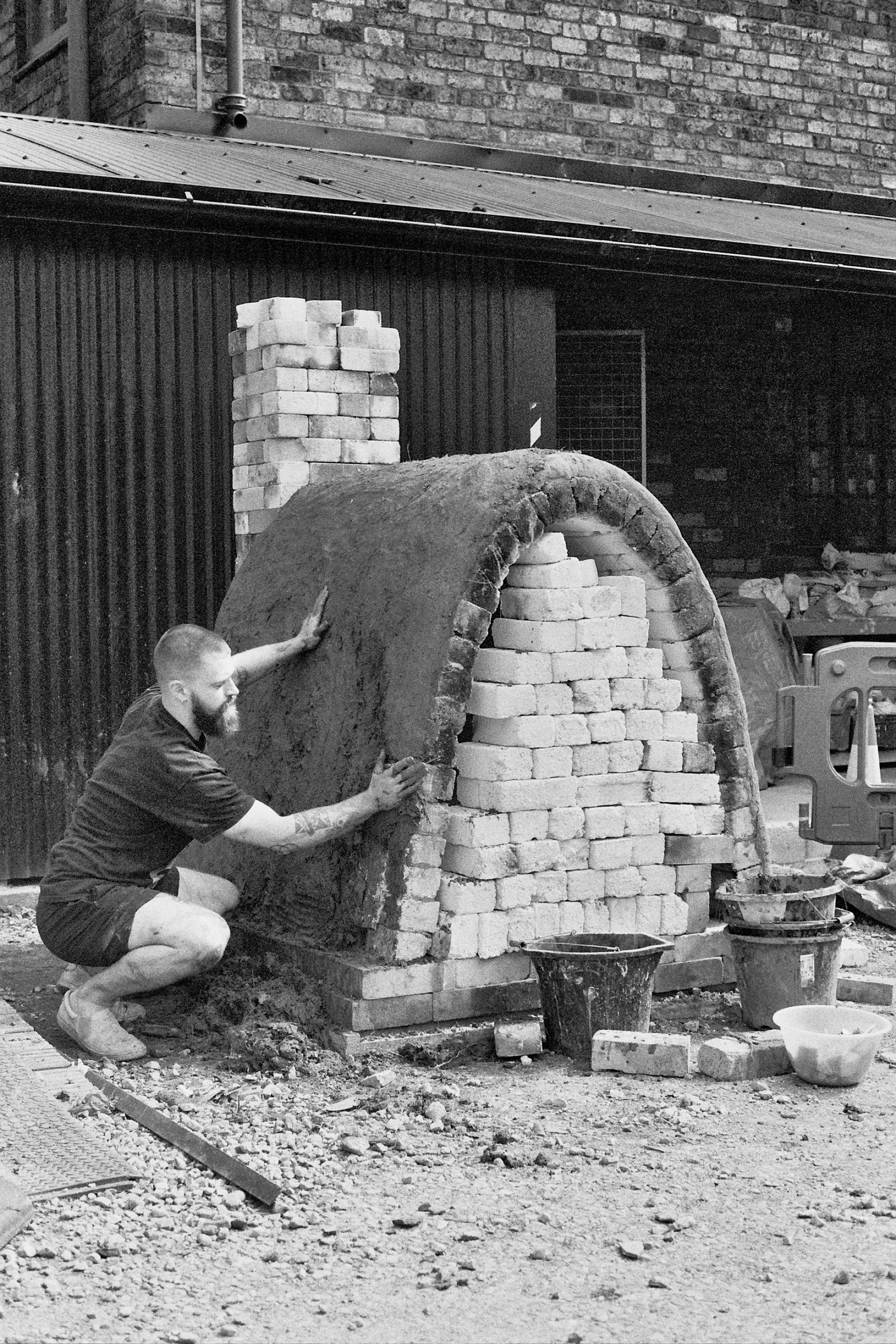

North Carolina
In Autumn/Winter of 2024 I spent time living with and working under established potter Matt Hallyburton in Burke County, North Carolina. The state has a unique geology highly suited to the potter interested in sourcing their own materials from nature, and the Catawba Valley is home to the only unbroken tradition of wood-fired, ash-glazed stoneware in Western culture. With an abundance of quality throwing clays and the recognizable “alkaline glaze” (pictured) composed of wood-ash, clay and glass cullet, North Carolina represents hundreds of years of ancestral knowledge of clay and fire.
During my time there I assisted Matt with the sourcing and processing of clay, production throwing, and firing his large Anagama. I participated in a number of wood-firings of unique North Carolinian groundhog kilns, which are not found outside of the country. I also participated in the testing and subsequent excavation of over 200 tonnes of a significant new source of potters clay discovered by Matt. I tested new glazes and clay recipes using the abundant natural resources, and gained invaluable experience in throwing, glazing and firing from Matt and his peers.




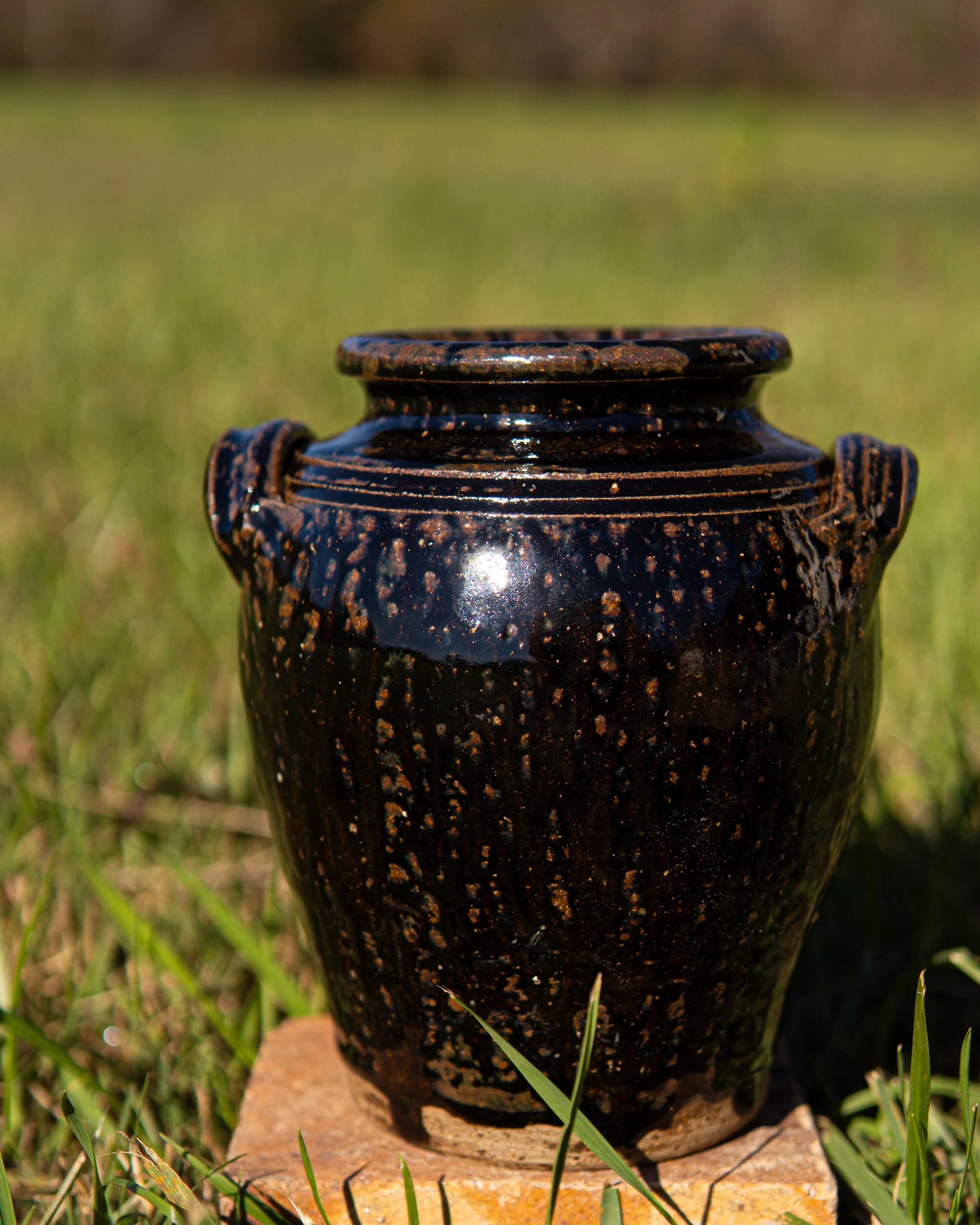


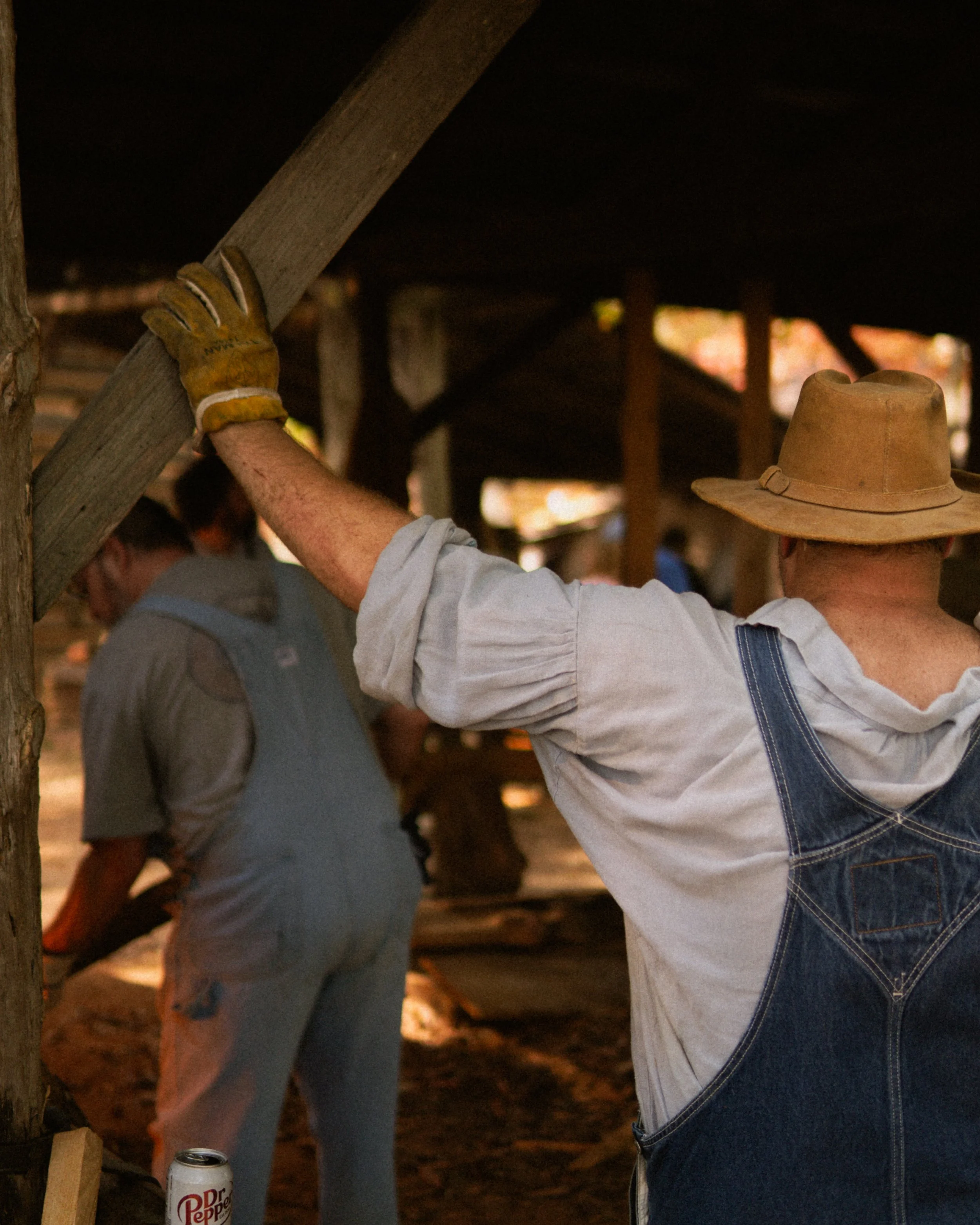
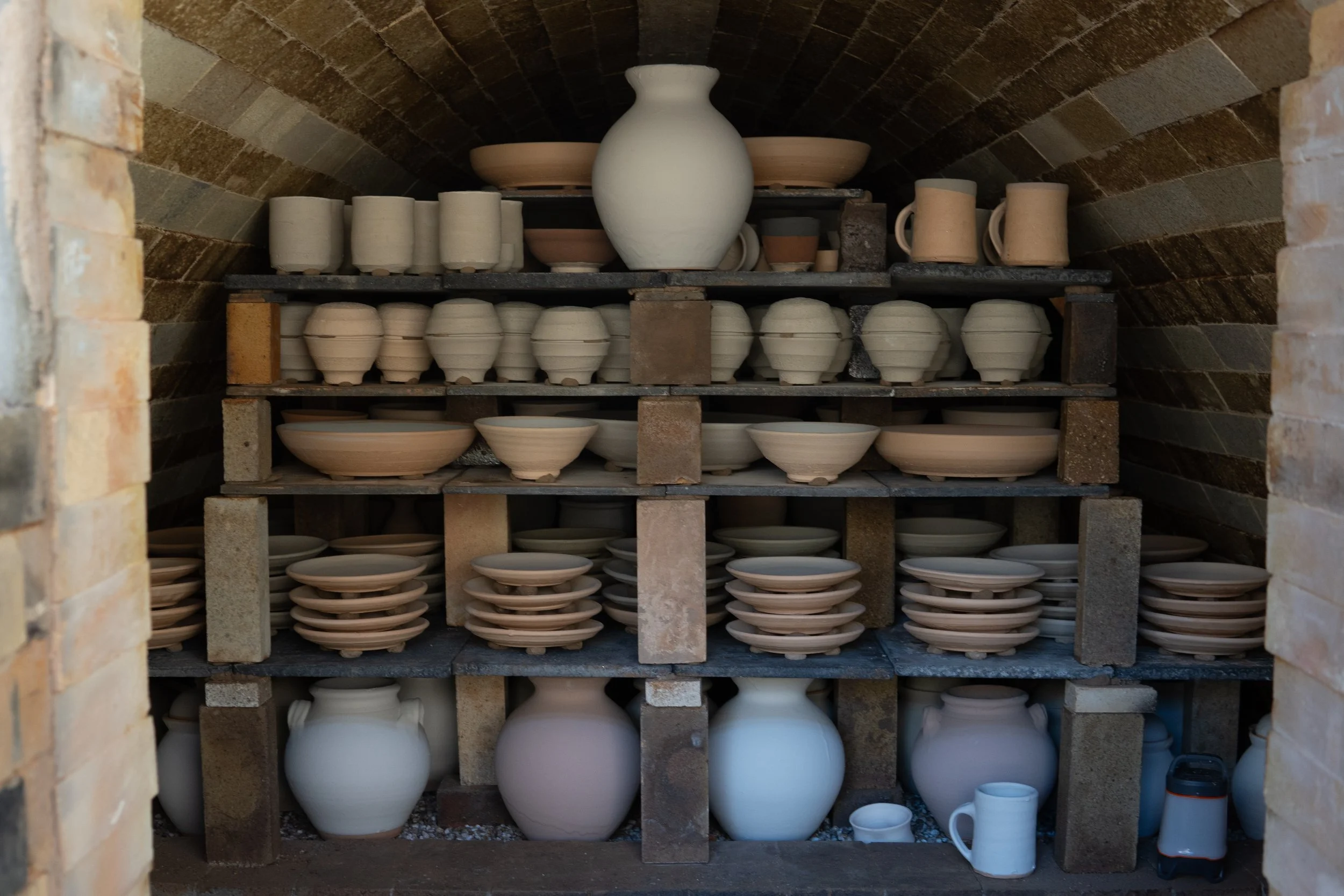


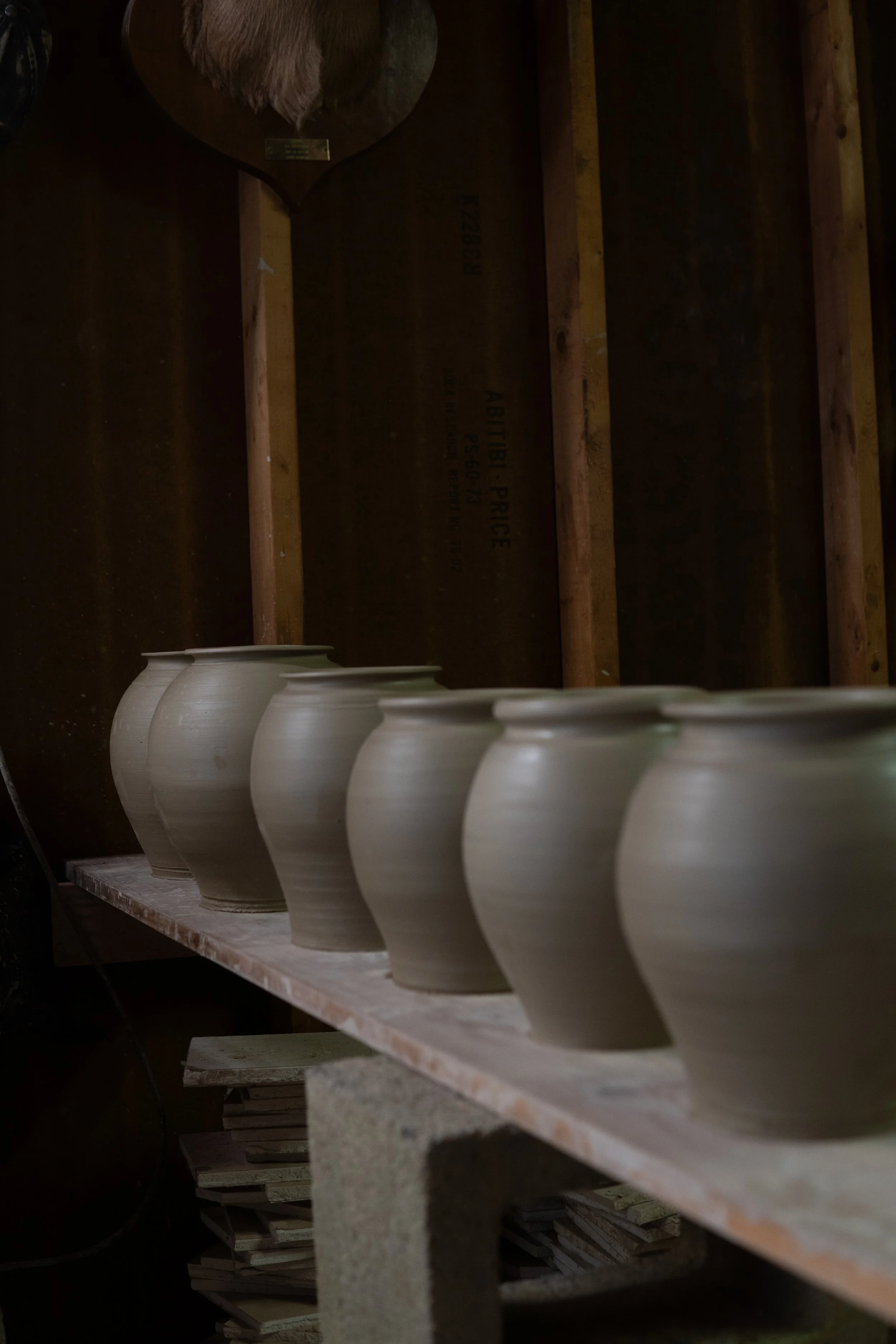




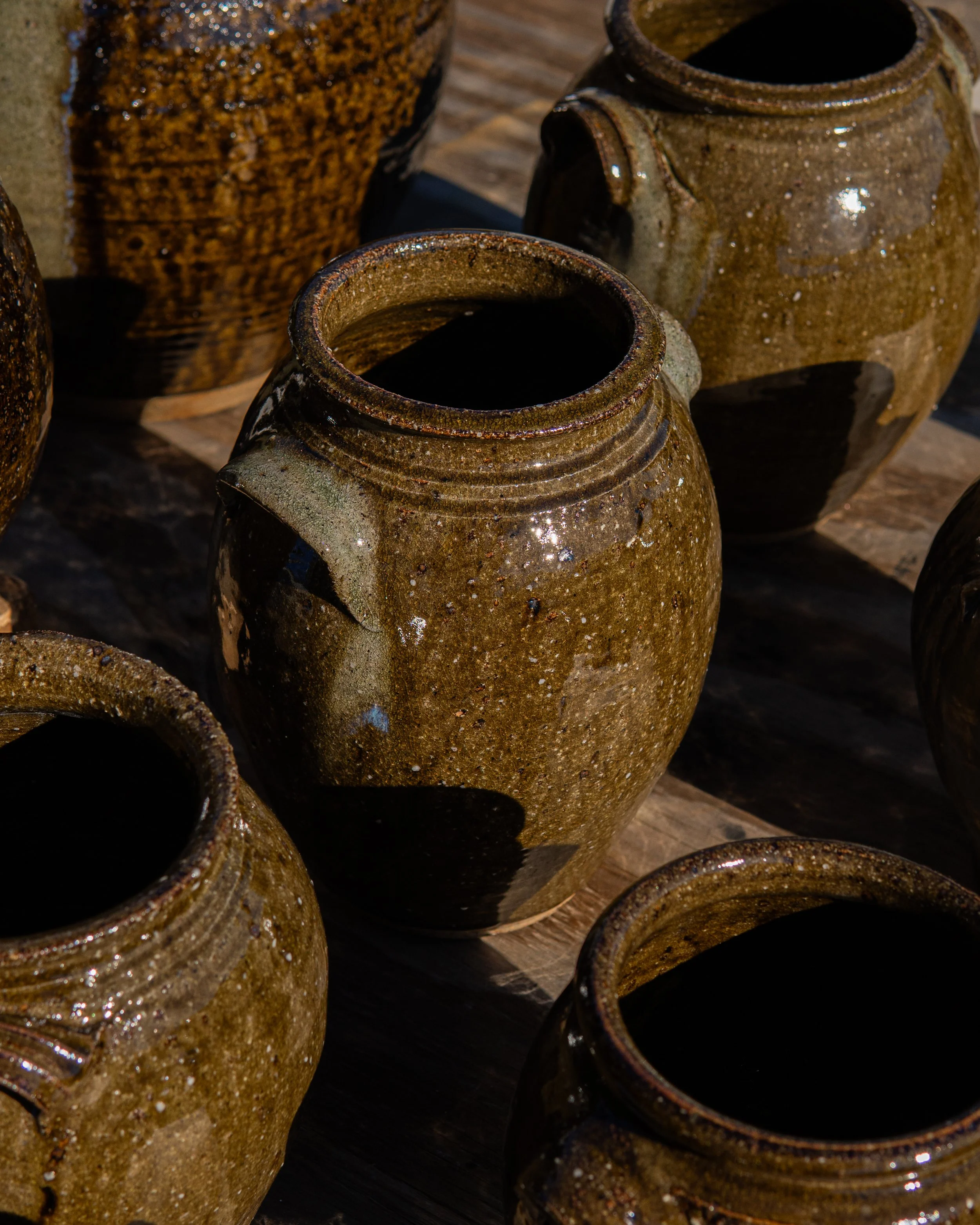


Potshop
Airspace Gallery, Stoke-on-Trent, 2023
For this group exhibition, I created a body of work focused on two clays which exist bordering one another in Hartshill Park, but have completely divergent properties. A dense, red marl and a crumbly, shale-ridden ochre had been revealed where a path was cut into a hill.
Following initial melt tests I formulated a dark stoneware body using the red clay, and a number of glaze recipes based around the yellow. These ranged from as much 3:1 clay/ash (mug, pictured adjacent) to recipes where the yellow clay and shale served as an addition in lower percentages.
Alongside the fired work, I exhibited the raw materials from which they were made in order to spark questions from observers. This is something which I have continued doing subsequently, and I always endeavour to display the work of nature alongside the fired piece to remind users of the geological process which preceded the pots existence.
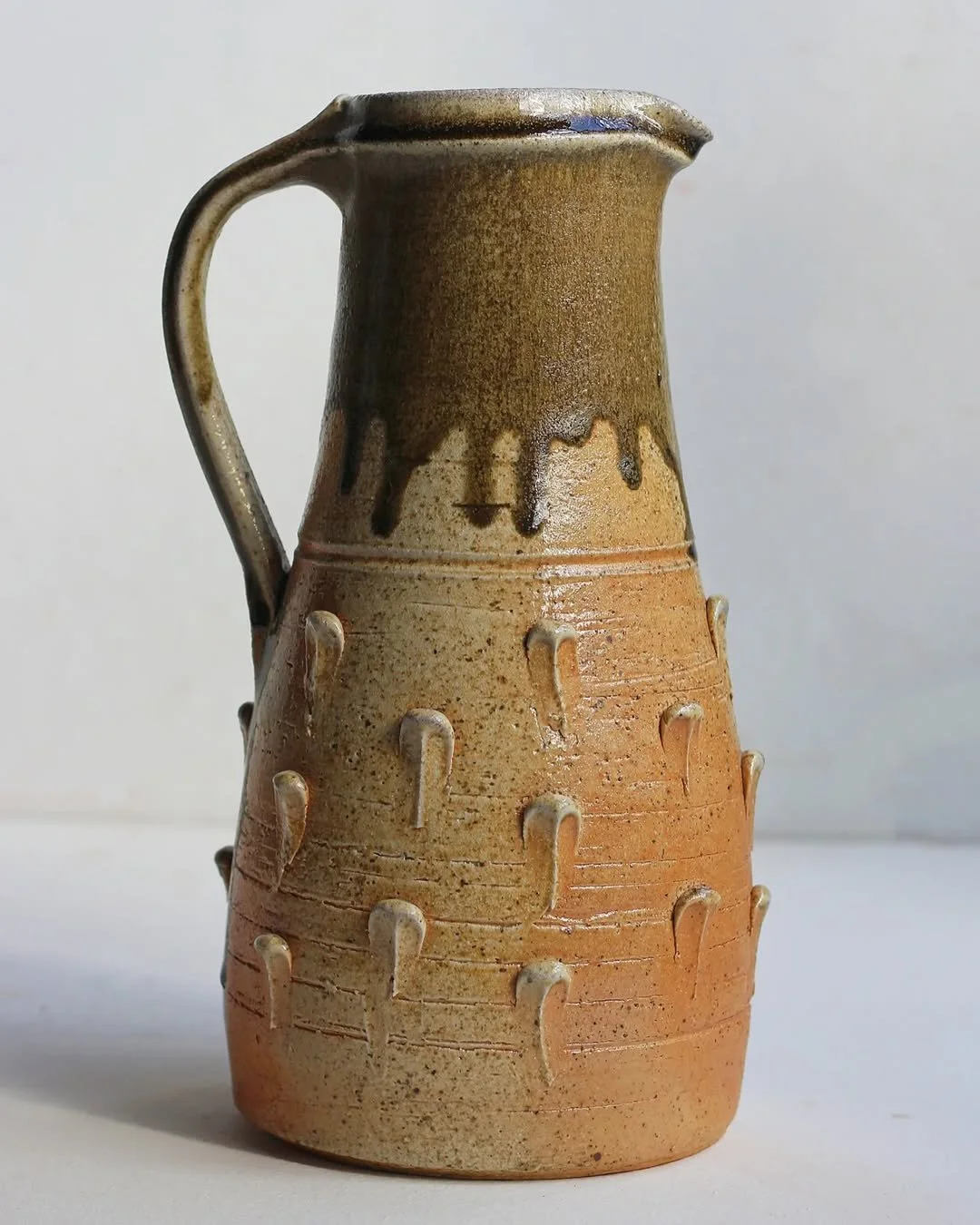
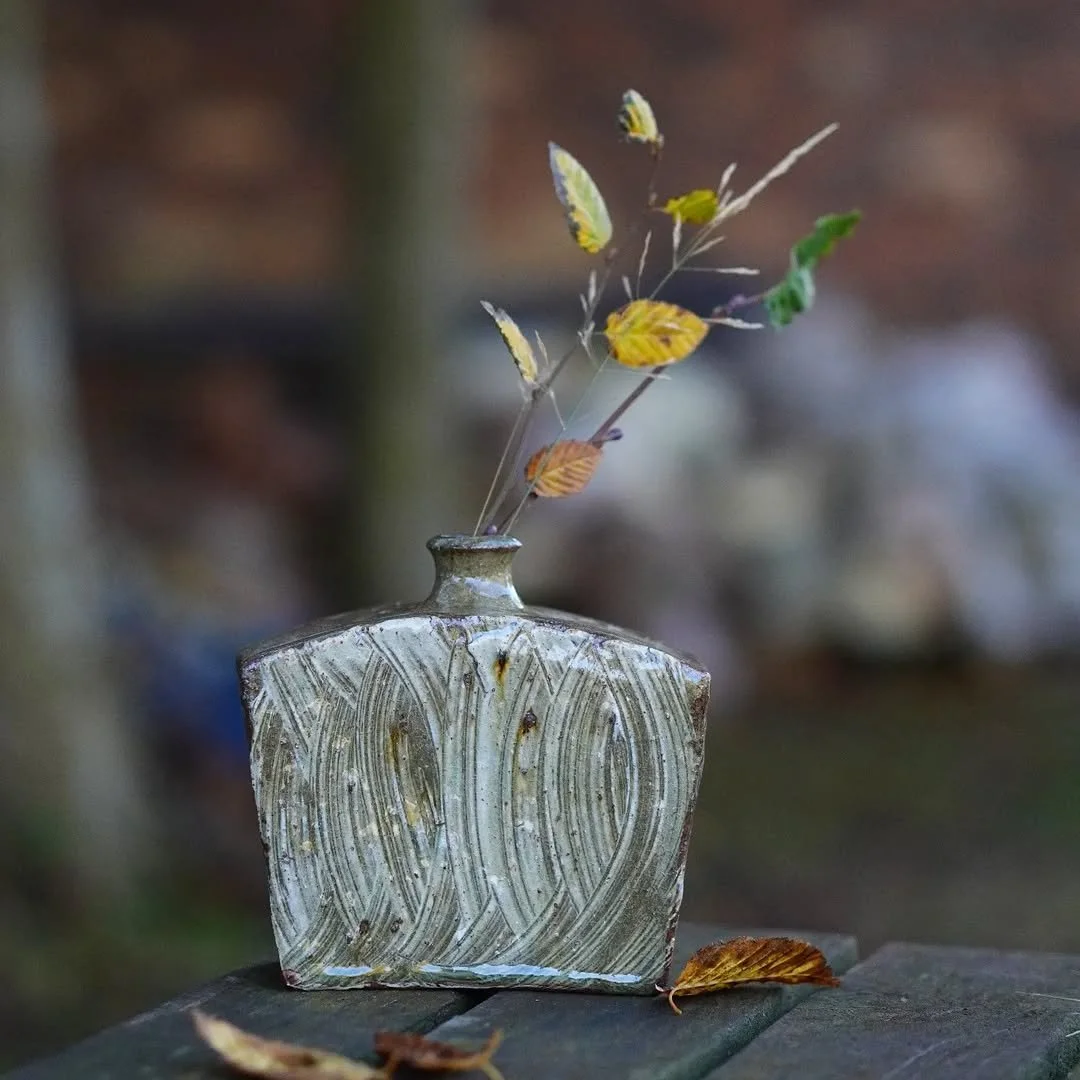
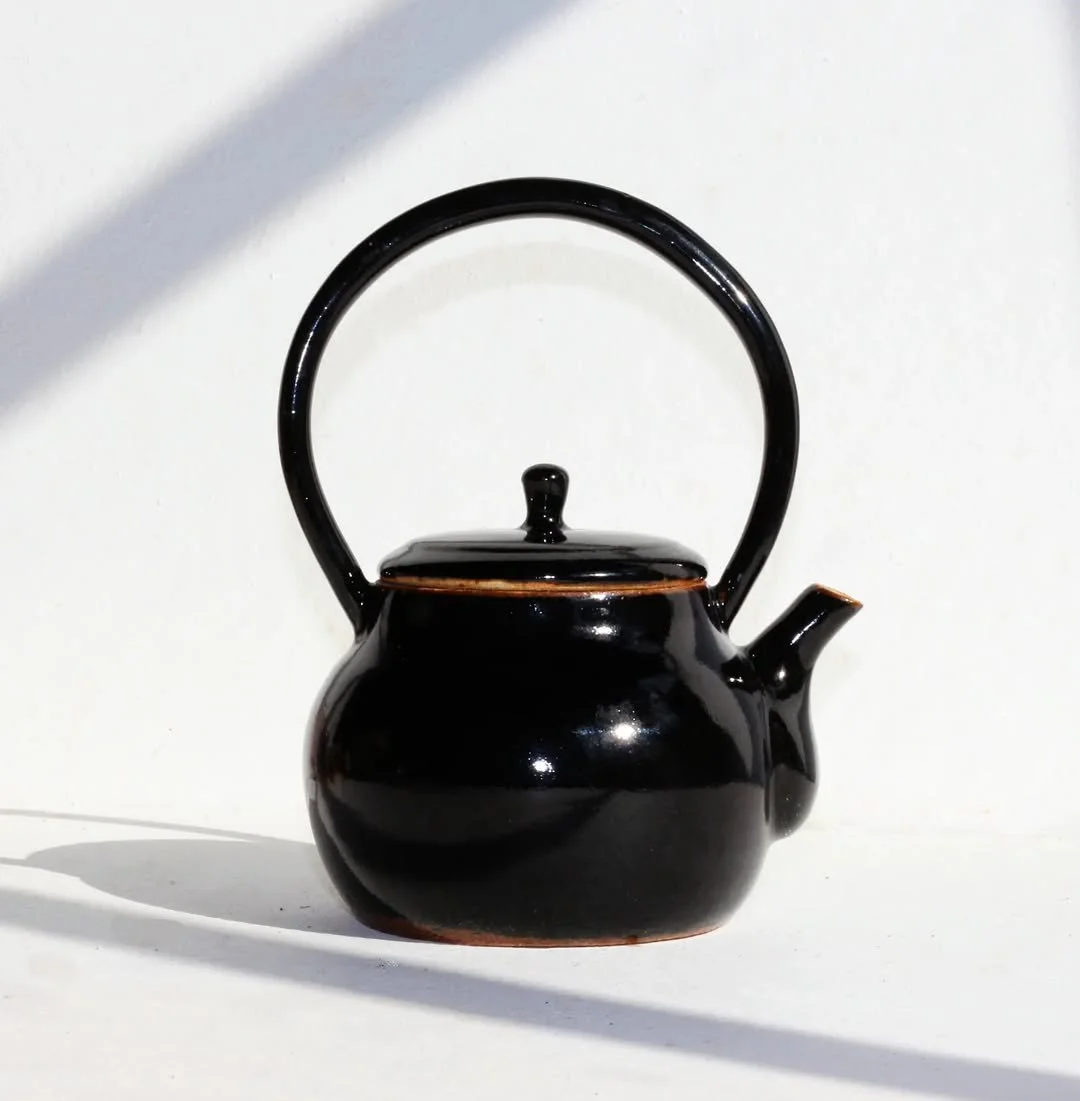


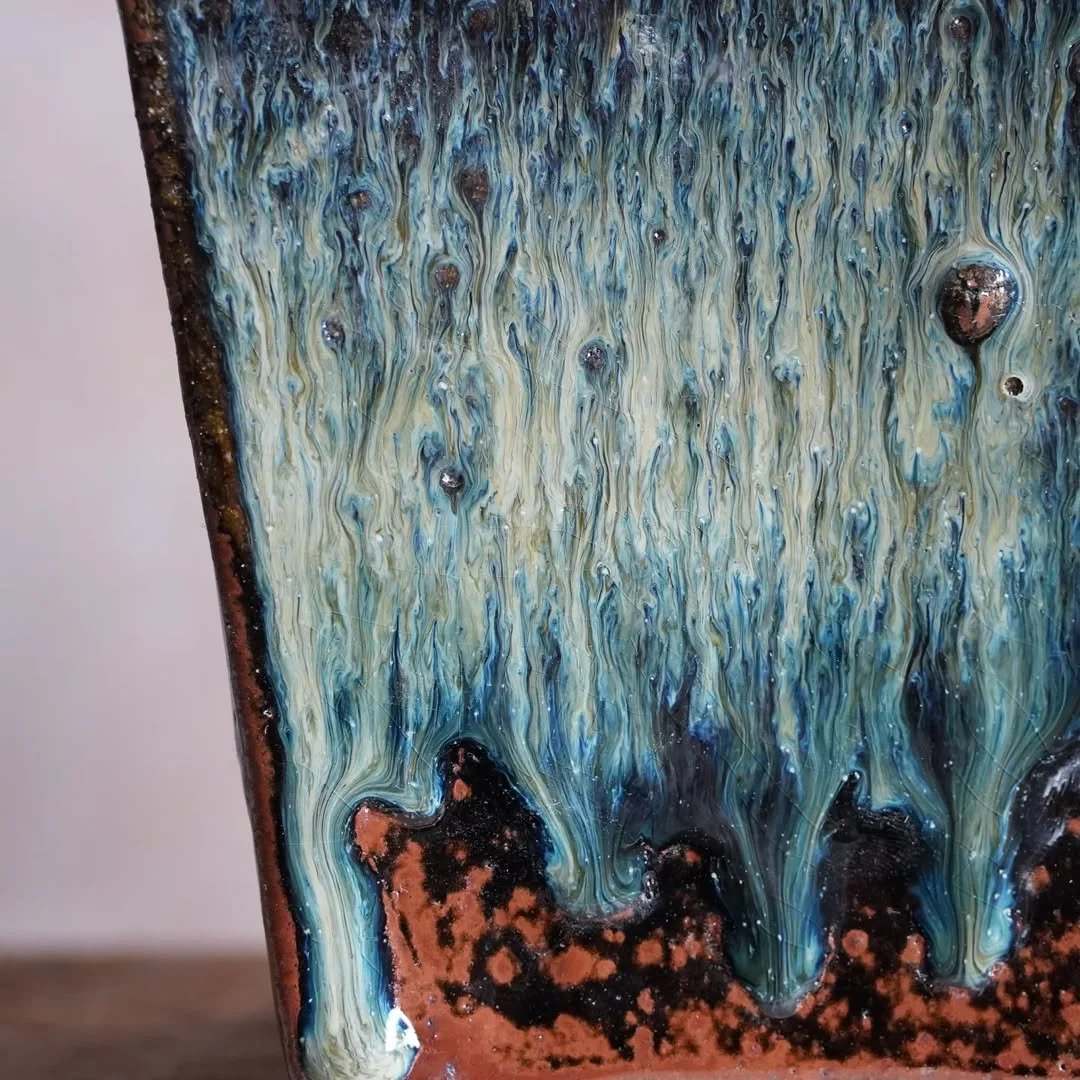
Glina 2024
Clay-dyed wool, linen, ceramic.
A collaborative piece made with textile artist and handweaver Nadine Wilde to accompany my graduation exhibition. The clay, sourced from a park in Stoke-on-Trent, was used to dye unprocessed Staffordshire sheep’s wool, which was then woven into a linen warp on a traditional tapestry loom. The header is made from the same clay, fired to 1260°C.
Both artists responded to the same material, exploring the possibilities which arise from combining and contrasting different crafts. Both the wool and the clay appear in varying states, the finished work both orderly and chaotic.
As craft practices become increasingly commercialised, fewer and fewer craftspeople come into contact with their raw materials as they are found in nature. This piece aims to provoke discussion around this by placing raw material and finished artwork on equal footing.
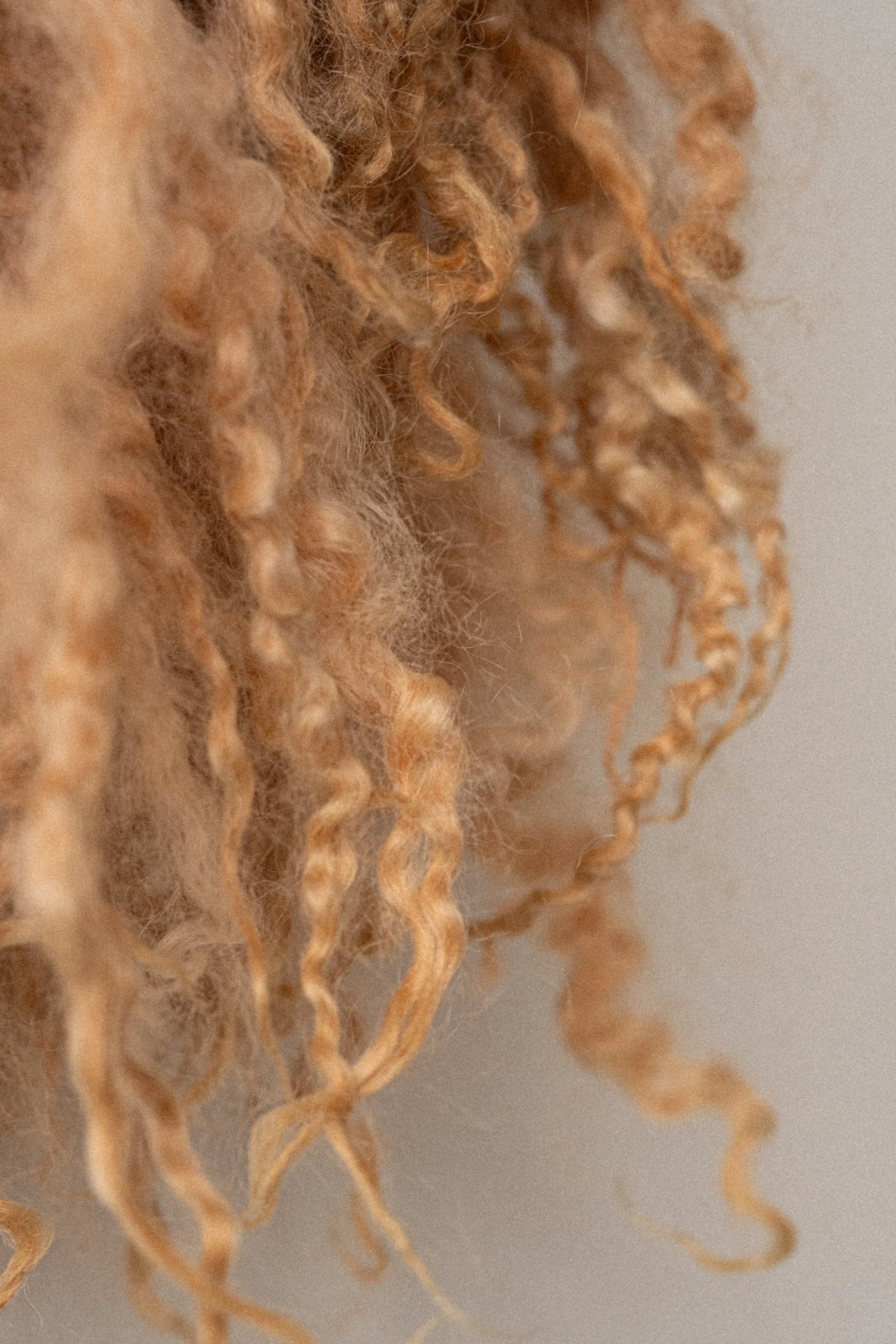

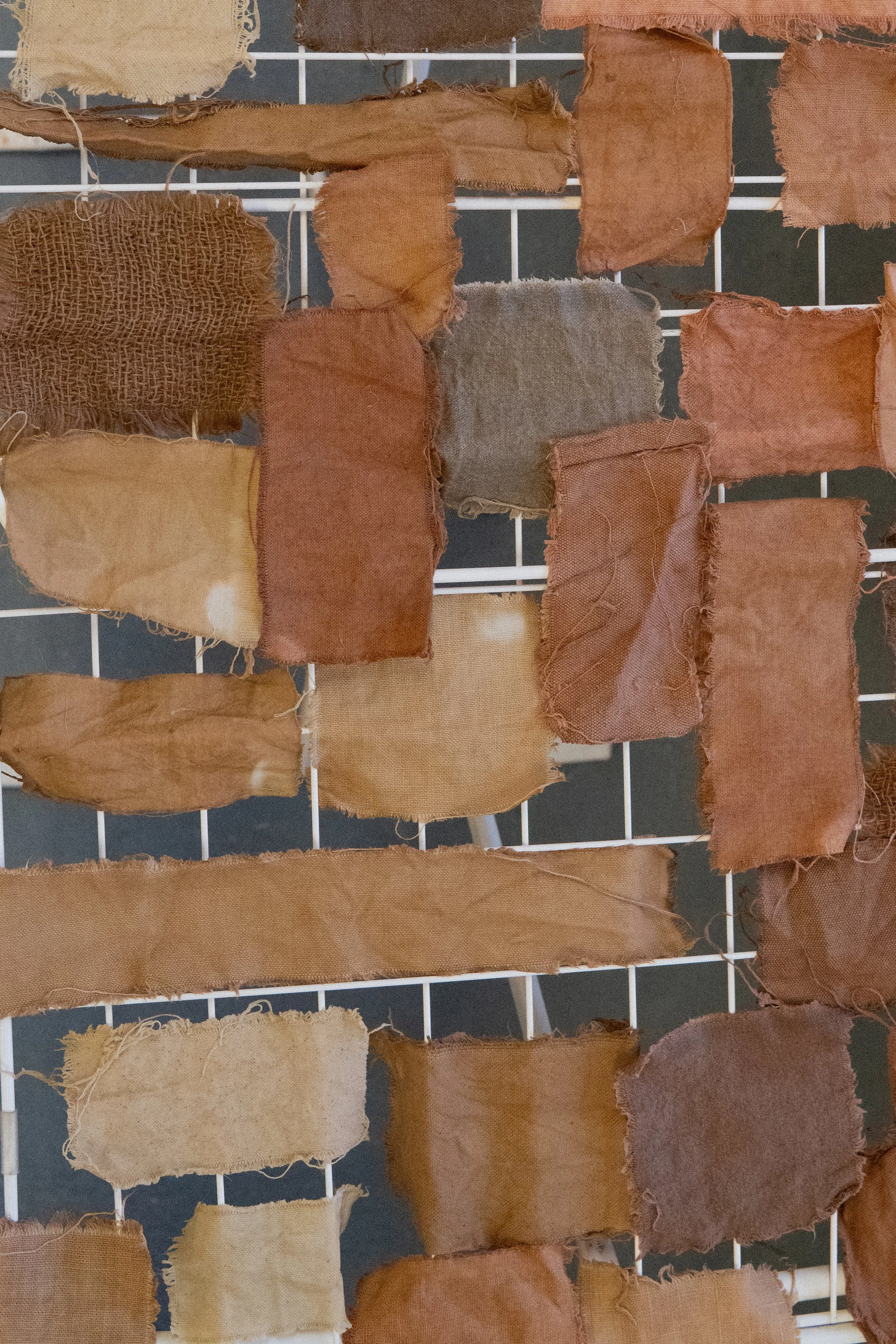
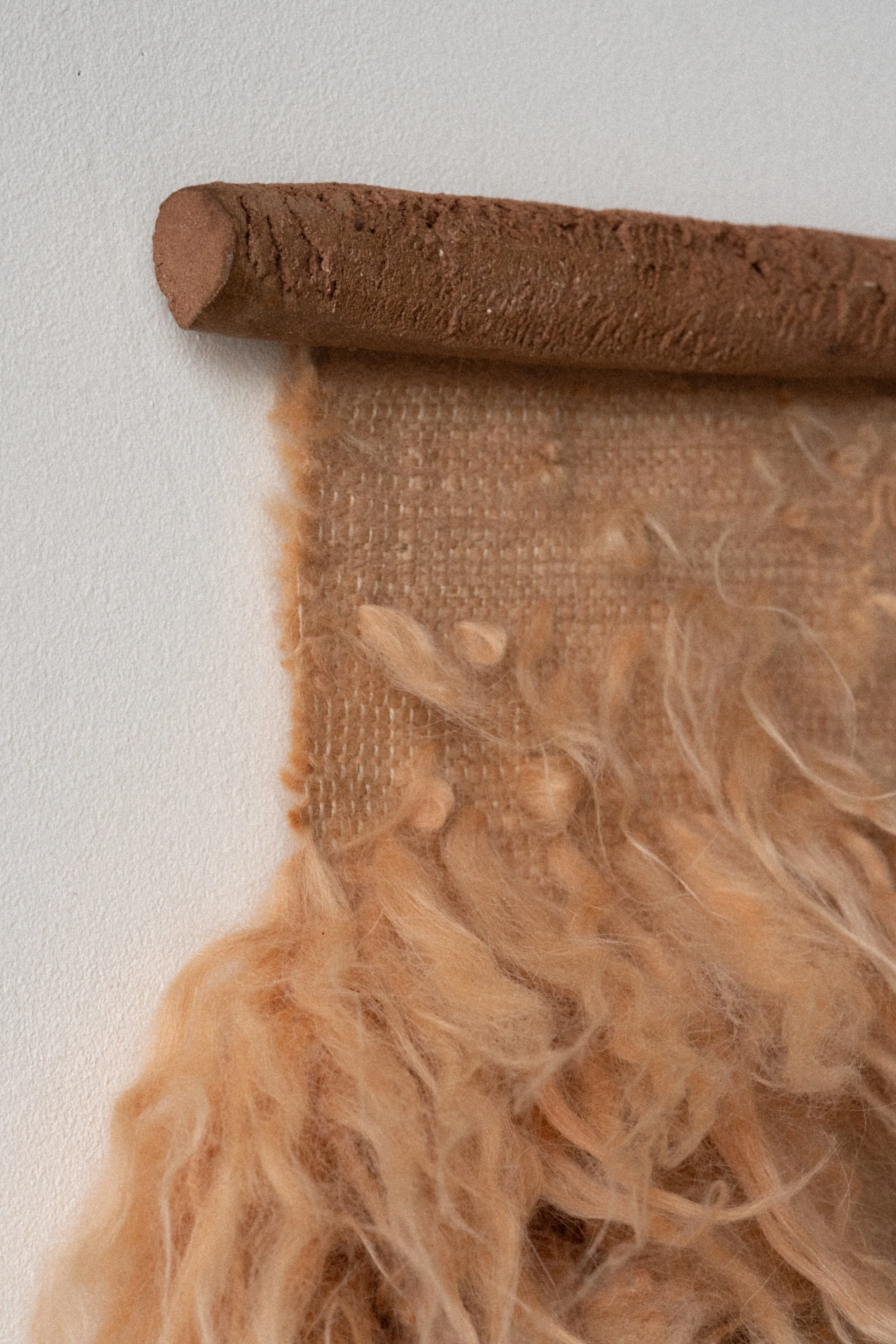

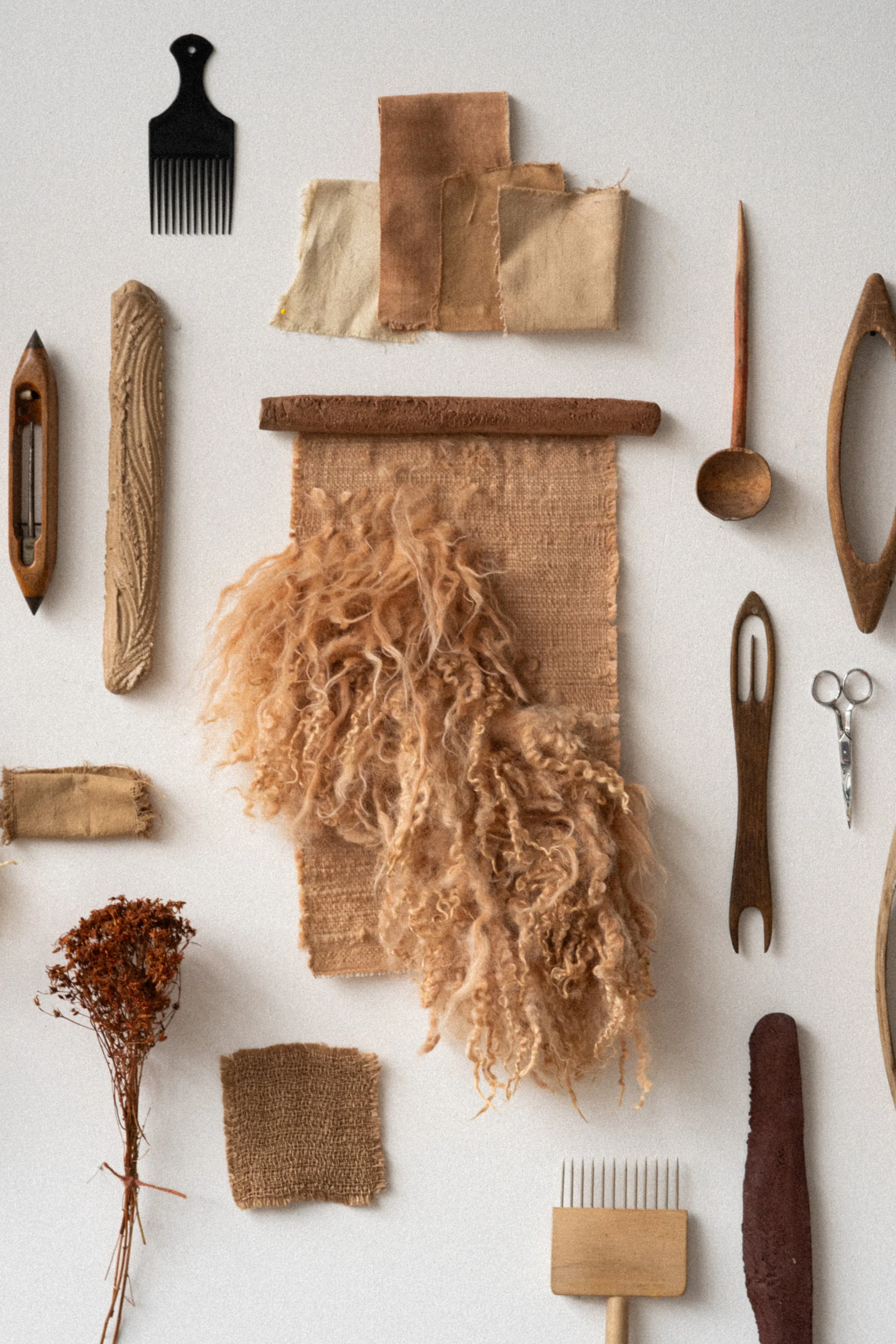

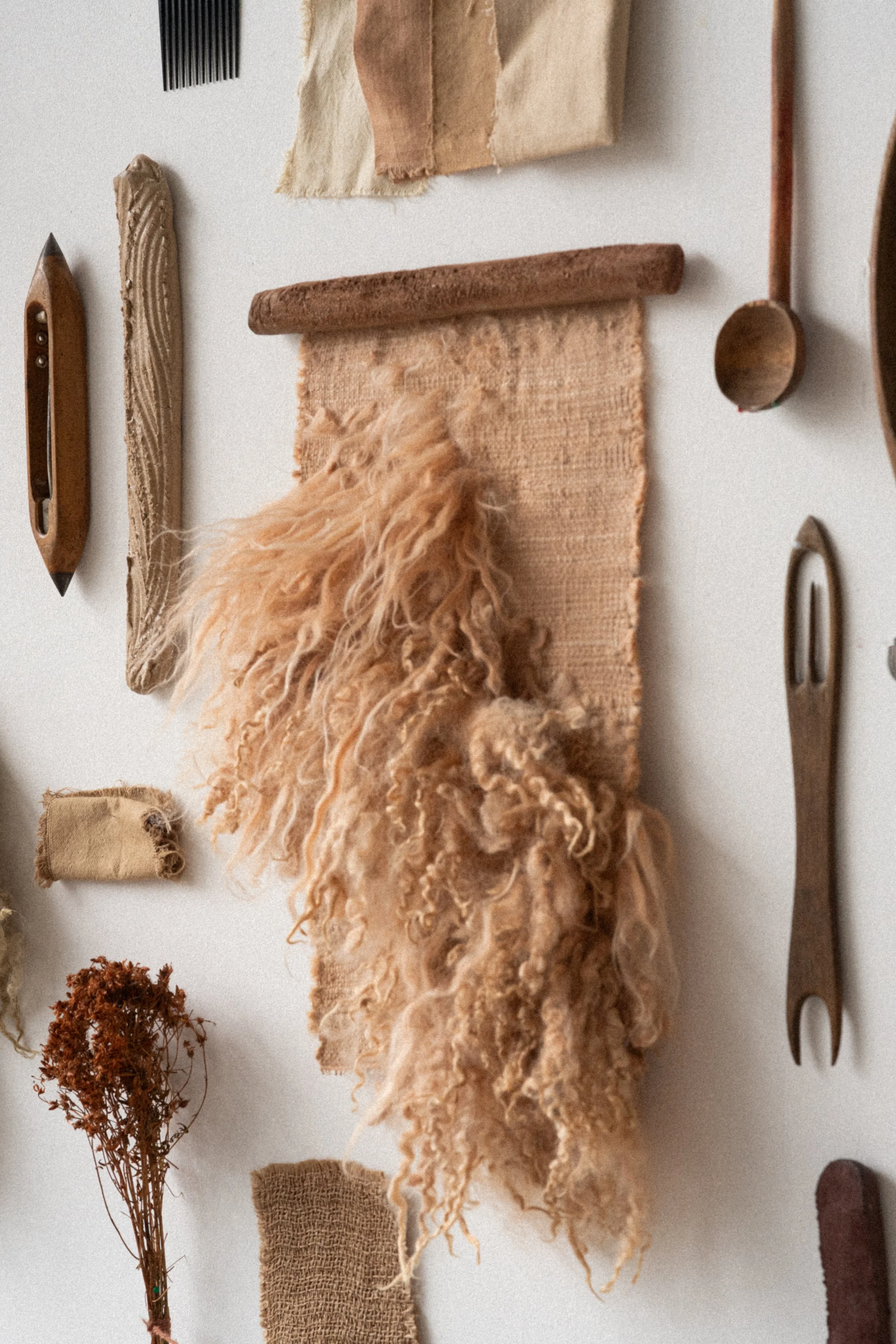
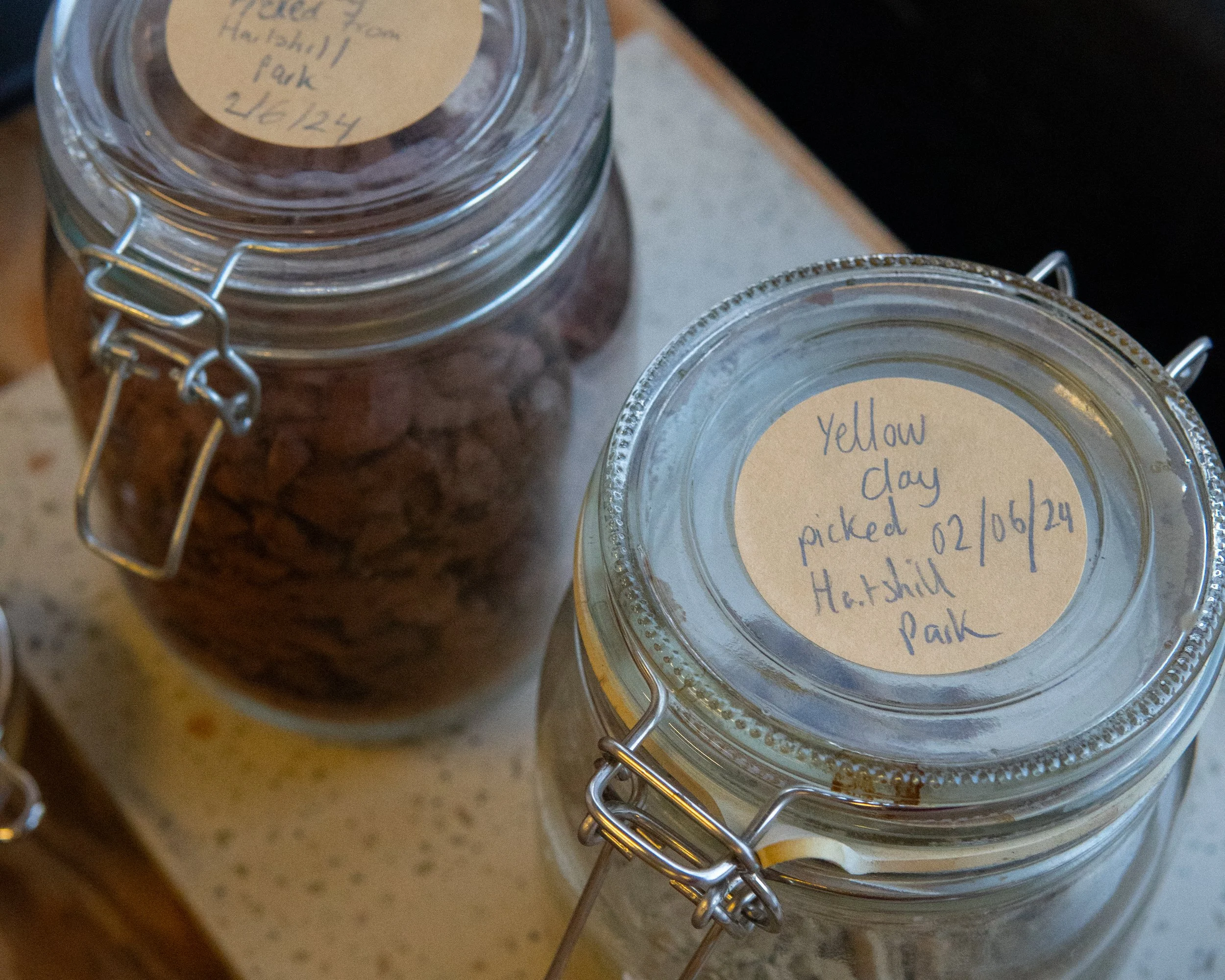
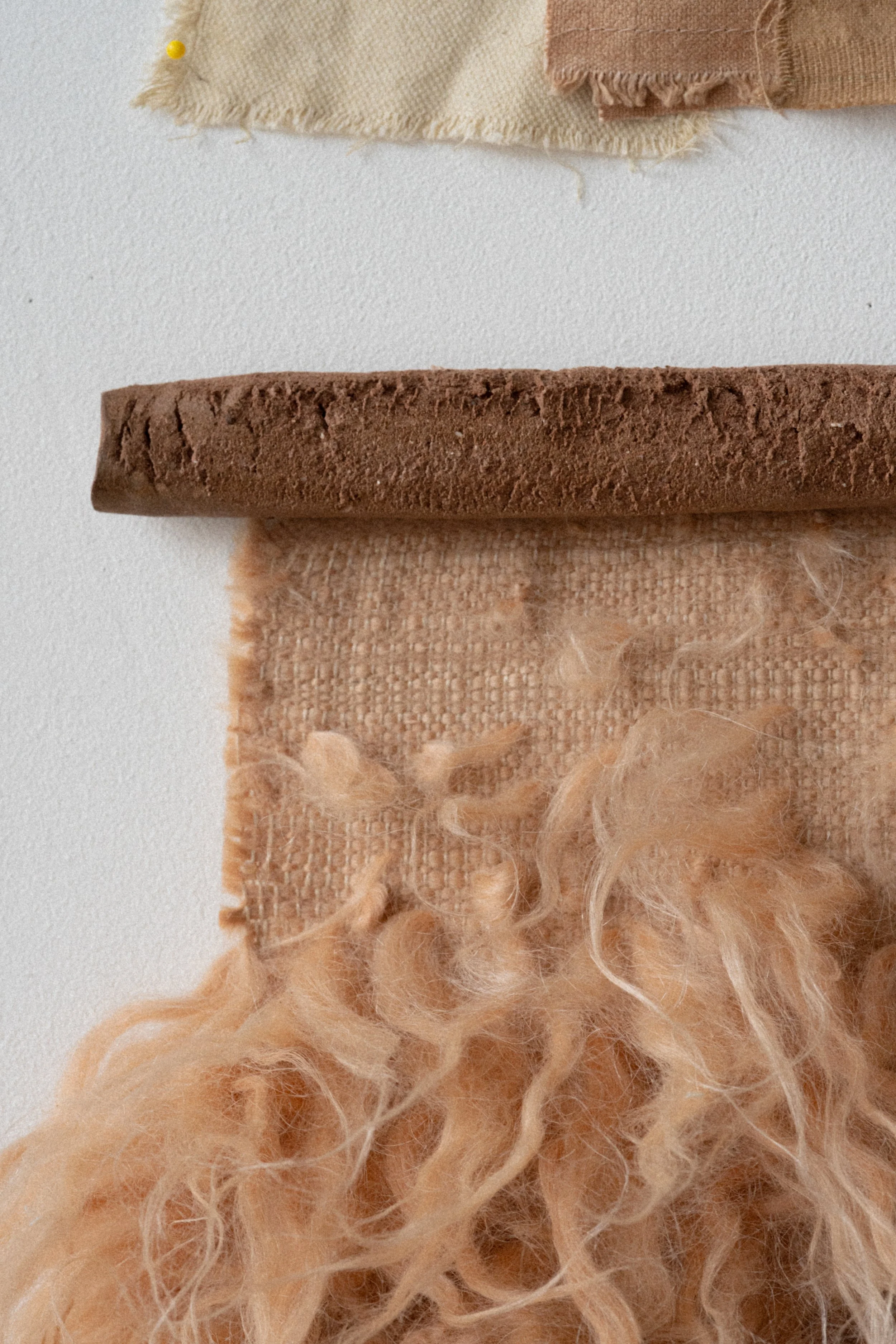
To see more of my work, please visit my Archive
Left: Undissolved silica within granite and ash glaze. Will Keating
Right: Satellite image of Thames Estuary. OLI/Landsat 8/NASA